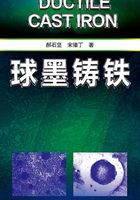
3.1 力学性能
3.1.1 拉伸性能
图3-1显示钢、球墨铸铁、灰铸铁受到拉伸时显示的拉伸应力-应变曲线。钢和球墨铸铁试样在一定应力范围内,应力和应变均按比例增加,两者呈直线关系。材料变形具有弹性性质。当应力达到比例极限,即发生弹性变形范围内所能承受的最大应力时,继续增加应力才开始出现塑性变形,显示应力-应变关系的直线将变为曲线,出现屈服现象。屈服现象出现使应力-应变之比减小。此时增加少量外力,将会产生较大永久变形。而含有片状石墨的灰铸铁,拉伸应力很低时就会发生塑性变形,因此应力-应变曲线几乎没有直线段和屈服点。

图3-1 钢、球墨铸铁、灰铸铁试样拉伸应力-应变曲线
1—低碳钢;2—珠光体球墨铸铁;3—铁素体球墨铸铁;4—无磁性奥氏体球墨铸铁;5—耐蚀奥氏体球墨铸铁;6—灰铸铁
珠光体球墨铸铁拉伸强度和比例极限高于铁素体球墨铸铁。拉伸时不出现明显屈服点,断裂前试样基本上沿全长出现均匀变形,无缩颈,断裂伸长率较低。铁素体球墨铸铁屈服现象出现较早。断裂前有缩颈发生,断裂后保留部分塑性变形。屈服强度和拉伸强度均低于珠光体球墨铸铁。
3.1.2 球墨铸铁的拉伸断裂
球墨铸铁中的球状石墨晶体内存在许多晶体缺陷,主要缺陷是小角度倾斜晶界。这种晶界是可移动的,移动时很少受到限制。当球墨铸铁承受的外力超过弹性极限时,球状石墨发生的可察觉变形显著增加。通常是使球体沿拉力方向伸长,侧向收缩(图3-2)。

图3-2 石墨球变形并互相连接
如果球状石墨被铁素体包围,铁素体晶粒发生晶内滑移继而出现塑性变形。晶粒也是沿拉伸方向伸长,侧向收缩。铁素体晶粒的变形量分布并不均匀,接近球状石墨的铁素体晶粒变形量大于距石墨球较远的晶粒变形量。这种变形状况,促使相邻石墨球互相接近,甚至互相连接。由于金属晶粒与石墨的变形率不同,在伸长方向的金属与石墨之间形成应力集中区,金属在该处出现缩颈现象并产生细微孔隙。
实验证实,铁素体球墨铸铁承受外加应力后的断裂出现在两种情况:一是在剪切应力作用下,缩颈区产生的细微孔隙发展成为裂纹;二是相连接的石墨球互相接近,最终连成一体,相当于形成较大的裂纹(图3-3)[1]。这两种裂纹扩展都能导致断裂。第一种情况萌生在石墨-铁素体界面上,扩展的所需能量较少,缩颈区裂纹扩展比较容易。第二种情况容易发生在石墨球呈线状排列的球墨铸铁中。

图3-3 石墨球互相连接形成较大的裂纹
石墨球均匀分布情况下,球数增多、间距减小并不意味着铁素体球墨铸铁拉伸强度必然降低。这是因为含有较多石墨球的铁素体基体吸收塑性变形能量的能力增强,可以抵消球间距减少所带来的不利影响。
在珠光体与铁素体混合基体组织中,通常是在两种组织的界面上萌生裂纹。由于两种组织的塑性变形抗力不同,界面处存在较大的剪切应力。珠光体的塑性变形量较小,难以使塑变区出现的应力得到恢复,因此,界面上的裂纹将在珠光体的层片间扩展。这种裂纹的扩展端既能穿过单个珠光体晶粒,也能沿珠光体团边界前进。
珠光体组织内含有层状碳化物,其裂纹在层片间以剪切方式扩展。在正应力作用下,金属晶体沿某些特定晶面分离而发生断裂。这种断裂属于解理断裂。这些晶面称为解理晶面。体心立方晶体中的(100)晶面和密排六方的(0001)晶面是最常见的解理晶面。球墨铸铁发生解理断裂之前没有明显的塑性变形。图3-4显示在一个珠光体团内裂纹扩展的方向大体上是平行的,能说明裂纹是在珠光体晶粒的层片间沿层片扩展方向扩展的。裂纹的扩展速度主要与珠光体的抗剪切能力有关。解理断裂所需要的变形能量和断裂能量都比较高。因此珠光体球墨铸铁比例极限、屈服强度、拉伸强度都大于铁素体球墨铸铁[2]。

图3-4 裂纹在层片间扩展
珠光体球墨铸铁宏观断口比较平整,有银灰色金属光泽。由于存在石墨,断口光泽和细密程度不如铸钢,在显微镜下可以清楚地看到珠光体解理断裂特征。铁素体球墨铸铁的断口比较粗糙,断面呈暗灰色,没有明显金属光泽,属于韧窝断口。
含有共晶碳化物和晶间碳化物的球墨铸铁,其裂纹萌生和扩展的过程与前两种方式不同。在拉伸试样的纵断面上观察,共晶碳化物与珠光体之间存在很薄的析出物,析出物可能是固态相变时碳化物分解产生的石墨薄膜。裂纹萌生在这些析出物上。这里存在偏析、夹杂物等,比较薄弱。此处裂纹优先沿晶界以类似解理方式扩展,扩展速度很快。
图3-5显示含有晶间碳化物的基体中裂纹萌生于碳化物,并在碳化物内扩展的情况。裂纹在碳化物中扩展速度很快,但是到达与碳化物相邻的铁素体界面时遇到阻力(裂纹在铁素体内扩展需要较大的能量),扩展速度减缓或停止。直到外加应力增加到一定程度,裂纹才继续扩展。由此可见,铁素体球墨铸铁中存在晶间碳化物对铸件力学性能是不利的。

图3-5 裂纹萌生于碳化物
3.1.3 球墨铸铁的拉伸强度
表3-1列出我国国家标准(GB/T1348—2009)中球墨铸铁主要室温力学性能指标。
表3-1 球墨铸铁单铸试块拉伸性能(GB/T1348—2009)

注:字母L表示该牌号有低温(-20℃或-40℃)冲击性能要求;字母R表示该牌号有室温冲击性能要求。
球墨铸铁的基体组织和球状石墨都对铸件力学性能产生影响。球墨铸铁中几种基体组织的拉伸强度以等温淬火产生的高碳奥氏体+针状铁素体组织为最高,其次为回火马氏体、珠光体、铁素体、奥氏体。具有各种基体组织的球墨铸铁拉伸强度和伸长率列于表3-2。含有较高拉伸强度基体的球墨铸铁一般来说都有较高的强度。同一类型基体可因组织状态不同而具有不同拉伸强度。珠光体组织的层间距决定其强度水平,组织越细密强度越高。
表3-2 各种基体组织的球墨铸铁拉伸强度与伸长率

球墨铸铁最小拉伸强度和相应的最小伸长率构成一条拉伸性能基线,按英制单位数据可将美国标准中5种牌号的球墨铸铁屈服强度与伸长率的关系绘成图3-6所示的曲线。曲线上的5个点分别表示120-90-02(淬火+回火)、100-70-03(全珠光体)、80-55-06(20%铁素体)、65-45-12(15%珠光体)、60-40-18(全铁素体)5种牌号的球墨铸铁力学性能。强度与塑性的相关方程为:
最小拉伸强度=36.8+126(%,最小伸长率)-0.61

图3-6 美国牌号球墨铸铁最小拉伸强度和相应的最小伸长率构成的拉伸性能曲线
球墨铸铁拉伸性能数据一般应在曲线之上。
拉伸性能曲线受铸件化学成分、热处理制度、铸件壁厚、加工硬化、石墨球数和石墨球化率等诸多因素的影响。
铸件化学成分是影响球墨铸铁拉伸强度的重要因素。常存元素中碳、硅、锰都有显著影响。适宜的碳当量和硅碳比都能提高球墨铸铁拉伸性能。本书将在各有关章节中进一步讨论这方面问题。
添加合金元素是改善球墨铸铁力学性能的有效技术手段。合金元素种类很多,其中很多都有改善力学性能的效能。
球墨铸铁拉伸性能对铸件冷却速度比较敏感。冷却速度较高时珠光体组织细化,拉伸性能较高。较薄铸件冷速较高,可以提高铸态拉伸强度。但过薄断面内可能出现碳化物。因此检测拉伸强度的试棒必须从与铸件断面尺寸相适应的部位切取。
热处理能够改善球墨铸铁拉伸性能。我们可以按铸件使用要求调整热处理规范而获得所需拉伸强度,效果十分明显。具有最高拉伸性能的高碳奥氏体+针状铁素体球墨铸铁就是通过等温淬火获得的,其拉伸强度已经超过1200MPa。
在超过屈服强度的应力作用下,材料塑性变形产生的加工硬化现象能使应力-应变比发生变化。每次施加的外力卸载后,试棒都出现一定的塑变并发生形变硬化作用,拉伸强度随反复加载次数增加而提高。强度较高的球墨铸铁受力产生的较低滑移量也能产生较高的硬化效应。在相同的变形量下,其屈服强度的提高比较明显。
球状石墨对力学性能影响主要因素是石墨球数和石墨球化率。石墨球数直接影响石墨球平均直径和间距。球数多则球间距减小,促进生成铁素体基体。
球化率对球墨铸铁拉伸强度和伸长率有一定影响。图3-7显示退火铁素体球墨铸铁的球化率与拉伸强度和伸长率的关系。可见伸长率和拉伸强度都有随球化率上升而提高。

图3-7 石墨球化率对拉伸强度和伸长率的影响
3.1.4 硬度
非合金球墨铸铁硬度值对拉伸强度、屈服强度和伸长率的影响如图3-8所示。对多组不同试样测定结果表明:试样硬度与屈服强度两者存在较近似的比例关系。但是,试样的化学成分(特别是含硅量),石墨球数、基体组织状态等因素都使这种关系发生一些变化。

图3-8 非合金球墨铸铁硬度值与拉伸强度、屈服强度和伸长率的关系
球墨铸铁的硬度取决于基体硬度。具有各种基体组织的球墨铸铁硬度如表3-3所示。
表3-3 各种基体组织的球墨铸铁硬度

硅对铁素体有固溶强化作用,能提高铁素体的硬度。硅对铁素体球墨铸铁硬度的影响如图3-9所示。

图3-9 硅对铁素体球墨铸铁硬度的影响
镍、钼、铜等能够强化和细化珠光体的合金元素,都能提高珠光体球墨铸铁的硬度。
热处理对改变球墨铸铁的硬度也非常有效。但由于球状石墨的存在,球墨铸铁淬火组织的宏观硬度比基体组织的淬火硬度略低一些。例如,淬火马氏体基体显微硬度为63~65(HRC),而经过淬火的球墨铸铁宏观硬度约为55~60(HRC)(根据铸件成分和厚度而不同)。
铸件硬度随温度变化而改变的情况如图3-10所示。图中四条曲线代表化学成分不同的球墨铸铁。但是硬度变化的趋势基本相同。420℃以前,温度对铸件硬度的影响较小。温度达到540℃后,共析组织开始球化。继续升温到650℃左右珠光体分解。因此铸件硬度随温度升高而不断降低。铸件中的硅和镍都有提高高温硬度的作用。

图3-10 不同温度下的铸件硬度
3.1.5 弹性模量
当金属承受外力时发生变形,外力撤去后变形随即消失,这种性质称为金属的弹性。所发生的变形称为弹性变形。发生弹性变形时的应力与应变量呈直线关系,遵循虎克定律。该直线的斜率(应力与应变量的比值)被称为该金属的弹性模量。弹性模量反映金属在弹性范围内抵抗外力作用下发生变形的能力。
基体组织性质及球状石墨能够影响球墨铸铁弹性模量。珠光体球墨铸铁正弹性模量高于铁素体球墨铸铁。在球墨铸铁中加入提高珠光体体积分数的元素能够提高材料的弹性模量。
减少球状石墨数量和体积分数都能提高弹性模量。
提高球化率能提高球墨铸铁弹性模量。如果组织中出现蠕虫石墨、碎块石墨或其他畸形石墨都会降低球墨铸铁弹性模量。图3-11显示球化率对弹性模量的影响[3]。

图3-11 球化率对弹性模量的影响
反复应变可导致材料强化,有助于提高材料弹性模量。材料本身温度较高时,弹性模量降低。
表3-4列出几种铸铁与45钢弹性模量的比值。由于球墨铸铁中有石墨存在,它的弹性模量低于正火45钢。
表3-4 几种铸铁与45钢弹性模量的比值

3.1.6 扭转、剪切、弯曲强度
扭转试验测得的球墨铸铁扭转强度、剪切强度都约为拉伸强度的90%。强度较高和韧性较低时差别更大。剪切屈服强度和比例极限值约为拉伸强度值的75%。
珠光体球墨铸铁扭转强度与拉伸强度接近。但它的扭转屈服强度比拉伸屈服强度低。两者相比约为0.70~0.77。铁素体球墨铸铁的这个比值略高一些。球墨铸铁承受扭力时具有较高的塑性,最大扭转角为灰铸铁的数倍。
珠光体球墨铸铁的抗弯强度极限大于1200MPa,与拉伸强度极限之比为1.4~1.5。
3.1.7 压缩强度
球墨铸铁压缩屈服强度比拉伸屈服强度高10%~20%。铁素体球墨铸铁压缩弹性极限应力比拉伸弹性极限应力高约20MPa。这是因为球状石墨的应力集中作用对材料拉伸时应力场的影响更为显著。
球墨铸铁在塑性变形区的应力-应变曲线因基体组织不同而有差别。变形抗力较大的珠光体球墨铸铁比铁素体球墨铸铁的曲线陡。无论变形产生于拉伸状态或压缩状态,情况都是类似的。
3.1.8 冲击韧度
冲击韧度反映材料在冲击载荷作用下发生断裂所能吸收的能量,也反映快速形变条件下,材料抵抗裂纹萌生、扩展和断裂的能力。
球墨铸铁的冲击吸收功与基体组织类型、铸件化学成分、球化率、石墨球数、热处理工艺、试样有无缺口等因素有关。
铁素体球墨铸铁的无缺口试样冲击韧度优于珠光体球墨铸铁。铁素体-珠光体混合基体组织的冲击韧度随珠光体含量增加而降低。各种基体的球墨铸铁无缺口试样常温冲击韧度列于表3-5。
表3-5 球墨铸铁无缺口试样常温冲击韧度

图3-12显示基体类型和试验温度对V形缺口球墨铸铁试样冲击吸收功的影响。反映出铁素体球墨铸铁韧-脆性转变温度最低,冲击吸收功最大。珠光体含量对球墨铸铁韧-脆性转变温度影响很显著,含量增加则转变温度提高。35%珠光体基体球墨铸铁转变温度一般是在室温以上。低温下基体组织的影响不太明显,但在室温下趋于明显,尤其铁素体球墨铸铁冲击吸收功对温度更为敏感。

图3-12 基体类型和试验温度对V形缺口球墨铸铁试样冲击吸收功的影响
铸件化学成分中,硅和磷对冲击韧度影响比较显著。硅含量增加对铁素体球墨铸铁V形缺口试样冲击吸收功和韧-脆转变温度的影响分别示于图3-13及图3-14。硅含量增加,韧-脆性转变温度提高。ω(Si)≈4%的球墨铸铁可用于耐热和耐蚀件,基体为铁素体,但室温脆性较大,在承受冲击载荷的工况条件下使用的铸件需要添加钼。

图3-13 硅对铁素体球墨铸铁V形缺口试样冲击功的影响

图3-14 硅对韧-脆转变温度的影响
磷量较高的球墨铸铁含有二元或三元磷共晶,这种高磷化合物在冲击作用下会成为裂纹萌生和扩展的优先位置,削弱球墨铸铁抗冲击能力。ω(P)>0.05%时,冲击韧性开始下降,超过0.08%时,下降就比较显著了。
铸件含碳量较高时,石墨球体积分数大,数量多,直径较大。受冲击时产生裂纹和裂纹扩展的塑性变形量较少,从而减少冲击吸收功。
大多数工程构件受冲击产生的断裂与一次冲击试样的断裂方式明显不同。工程构件断裂通常是小能量多次冲击导致裂纹形核和扩展的结果,这是一个损伤积累的过程。一次冲击断裂和多次冲击断裂的机制和主导因素不同。多次冲击抗力主要取决于材料强度和塑性的综合性能。除了强度影响外,材料断裂时所能吸收的塑性功也是抗断裂能力的主要因素。图3-15显示45号钢(曲线1)、铁素体球墨铸铁(曲线2)、石墨球粗大的混合基体球墨铸铁(曲线3)的冲击功与临界冲击次数曲线(A-N曲线)。

图3-15 球墨铸铁和45号钢的A-N曲线
1—45号钢;2—石墨球细小;3—石墨球粗大
冲击能量较高时,球墨铸铁多次冲击抗力比45号钢差,冲击能量较低时,球墨铸铁多次冲击抗力接近或超过45号钢。一般工程构件大部分是承受多次冲击,说明球墨铸铁件在较低冲击载荷作用下有一定的安全可靠性。
珠光体球墨铸铁的冲击韧度低于中碳钢,影响小能量多次冲击韧度的各种因素都与材料所承受的冲击能量有关。冲击能量较大时,多次冲击韧度受材料的塑性影响较大,凡能提高塑性的因素(铁素体基体、含硅量较低、石墨球细小均匀)都能提高多次冲击韧度,冲击能量较小时,材料强度是影响多次冲击韧度的主要因素。提高强度则多次冲击韧性提高。珠光体球墨铸铁在较低冲击能量作用下,其小能量多次冲击抗力优于中碳钢。
3.1.9 疲劳极限
机器零件经过多次交变应力循环作用下,可能在应力水平低于拉伸强度(σb),甚至低于屈服强度(σ0.2)情况下损坏。这种损坏属于疲劳损坏。对于球墨铸铁光滑试样来说,疲劳损坏前应力循环次数可以达到107次,不出现明显的塑性变形,而是突发的断裂失效。从断口上可看到裂纹起点和以此为中心向周围扩展的层状纹理,纹理范围以外的断面比较粗糙。
通常以经受107次交变应力而不发生疲劳断裂的最大应力值来表示材料的抗疲劳断裂能力,称为疲劳极限。根据应力作用方式不同,有循环对称弯曲疲劳极限、拉压疲劳极限、旋转弯曲疲劳极限、冲击疲劳极限、接触疲劳极限、腐蚀疲劳极限等。
球墨铸铁疲劳断裂过程和其他金属材料一样,包含裂纹形核和扩展两个基本过程。
在交变应力作用下,材料内部应力最集中的薄弱部位常是裂纹萌生部位。在球墨铸铁中,由于球状石墨和其周围基体变形不同而形成的空洞前端,往往是应力最集中的部位。首先出现的裂纹是在几个晶粒之间受力发生滑移时产生的。形状不规则的石墨、夹杂物和缩孔、缩松的边缘,也是裂纹可能优先萌生的位置。
拉压应力产生的裂纹只在拉应力下扩展。其途径与在静载荷下裂纹扩展的途径很类似。裂纹扩展与基体类型有关。前期扩展速率较小。这一阶段的显微特征是使断口上出现大量相互平行的纹理(一般称为辉纹)。辉纹密度与疲劳产生的宏观裂纹扩展速率有关。裂纹扩展速度随交变应力次数的增多而加大。
裂纹扩展使零件承载断面逐渐减小,当减小到超过其承载能力时,裂纹由亚稳扩展转变为失稳扩展,失稳扩展表示裂纹在短时间急剧扩张而导致零件断裂。失稳扩展阶段形成的断口粗糙,晶粒粗大。
图3-16为φ10mm珠光体球墨铸铁试棒内部疲劳裂纹长度与交变应力循环次数的关系。由图可见试验期内大部时间消耗于使裂纹扩展至0.1~0.2mm阶段。一旦裂纹达到这个尺寸后,其扩展速度显著加快。

图3-16 φ10mm珠光体球墨铸铁试样内部疲劳裂纹长度与交变应力循环次数的关系
退火铁素体球墨铸铁所受交变应力与疲劳断裂前所经受的应力循环次数之间的关系示于图3-17。图中显示光滑试样的疲劳极限值(σ-1约197MPa)比缺口试样的值(σ-1约120MPa)高。说明疲劳极限对缺口是敏感的。

图3-17 铁素体球墨铸铁交变应力与循环次数关系
材料的疲劳极限随其抗拉强度而提高。球墨铸铁抗拉强度与疲劳极限比(疲劳极限与拉伸强度极限之比)之间的关系如图3-18所示。

图3-18 球墨铸铁抗拉强度与疲劳极限比之间的关系
碳当量相同的铸铁中,相邻球状石墨之间的距离大于相邻片状石墨之间的距离。而且球数减少,距离增大,交变应力产生的裂口扩展路径增大。在条件相同情况下,球墨铸铁中裂口扩展所对应的循环次数多于灰铸铁。在探查球墨铸铁疲劳裂纹扩展过程时发现,如果球状石墨周围应力集中比较轻微,则相邻石墨腔体有遏制裂纹扩展的作用,可提高铸件抗疲劳能力。
旋转弯曲疲劳极限是许多球墨铸铁件的重要力学性能指标。图3-19显示球墨铸铁基体硬度对其旋转弯曲疲劳极限的影响[4]。铸件硬度低于500(HV)时,旋转弯曲疲劳极限随基体硬度增加而提高。这是因为晶体滑移阻力随硬度上升而增加,推迟了裂纹萌生并减缓了裂纹亚稳扩展速率。

图3-19 基体硬度对其旋转弯曲疲劳极限的影响
石墨球尺寸对旋转弯曲疲劳极限的影响示于图3-20中。影响程度与基体硬度有关。

图3-20 石墨球尺寸对旋转弯曲疲劳极限的影响
畸形石墨降低球墨铸铁的旋转弯曲疲劳极限和强度。但是对强度的影响比较大,对疲劳极限的影响相对较小。ω(C)=3.70%、ω(Si)=2.50%、ω(Mn)=0.60%球墨铸铁球化率由98%降到50%时,其抗拉强度降低了1/3,疲劳强度只降低约25%。上述成分的球墨铸铁球化率对疲劳极限的影响如图3-21所示。

图3-21 球化率对疲劳极限的影响
球墨铸铁件表面状况(粗糙度、硬度、表面残留应力)对其疲劳极限也有明显影响。采用喷丸表面强化、表面淬火、表面滚压强化等工艺措施都能使球墨铸铁件表面在外加压力下产生局部塑形变形,形成残余压应力,从而改善零件的抗疲劳能力。
3.1.10 断裂韧度
人类历史上曾经出现过多起产生原因当时不被人们认识的事故。一些重型设备上的金属构件在低于许用应力下正常运行时突然发生脆性断裂。科学工作者对于此种现象进行深入研究后发现,脆性断裂与金属冶金质量、内部缺陷以及异质物的存在有关。材料内部的夹杂物、显微孔洞易于在材料中萌生细微裂纹。这些细微裂纹在外加负荷(特别是交变载荷)或腐蚀性介质作用下,经过亚临界扩展发展为失稳扩展(加速扩展),最终形成宏观裂纹,导致构件发生脆性断裂。
科学工作者应用弹塑性力学理论研究了裂纹萌生和扩展的规律及其影响因素。推导出“断裂韧度”概念,并把断裂韧度视为材料性能的一项指标。这个指标的意义在于:它以数学方式表达了含有内部缺陷的零件承受张开性负荷时,避免发生裂纹失稳扩展的裂纹尺寸和所受应力的关系。具体来说,在一定加载方式下,把裂纹尺寸的平方根与所承受应力的乘积值作为避免这种失稳扩展的基础临界数据。把此数据定义为应力场强度因子,以KI表示。当KI值达到导致裂纹开始失稳扩展的临界值时,此特性参数写为KIC。KIC=MPa·m1/2。其中MPa为加在裂纹范围内的应力,m与裂纹长度有关。KIC代表不发生裂纹失稳扩展时金属材料所允许的最大韧度,也称为平面应变断裂韧度。按标准方法试验得出的KIC值通常被简称为材料的断裂韧度。在实际工作应力状况下,可以利用这个因子计算出避免发生突然脆性断裂的最大内部裂纹尺寸和应力。
断裂韧度与传统力学性能指标不同之处在于:前者是在预制裂纹试样上测定,后者则是在未顾及内部缺陷的光滑试样(或缺口试样)上测定。传统指标中强度和塑性指标是分开的,断裂韧度则是强度和塑性的综合指标。例如已知裂纹长度可求出避免材料发生脆性断裂最大应力。已知应力(σ)时可求出避免材料发生脆性断裂的最大裂纹长度。
球墨铸铁的断裂韧度(KIC)受基体组织、热处理状态、石墨球化率及分布状态、试验温度等诸多因素的影响。几种基体组织的球墨铸铁KIC值列于表3-6。
表3-6 几种基体组织的球墨铸铁KIC值

珠光体球墨铸铁是通过解理断裂而失效,呈现平滑的解理断口。珠光体的层片间距对KIC值有影响。层片间距越小,即珠光体越细,对裂纹在其中萌生和扩展的阻力越大,因而材料的断裂韧度相应提高。铁素体球墨铸铁断裂前有大量塑性变形,裂纹很不规则,呈波浪形。
图3-22显示三种基体球墨铸铁在应力强度因子范围ΔK相同情况下裂纹扩展速率的比较。可见珠光体球墨铸铁的裂纹扩张速率最高,铁素体球墨铸铁的裂纹扩展速率最低,奥氏体+针状铁素体球墨铸铁介于两者之间。

图3-22 几种基体球墨铸铁裂纹扩展速率(11760N/1960N)的比较
P—珠光体球墨铸铁;F—铁素体球墨铸铁;A+B—奥氏体+针状铁素体球墨铸铁
热处理对球墨铸铁断裂韧度有一定影响。淬火后材料的KIC值将要降低。但继之以高温回火使材料具有细珠光体组织,则KIC值显著提高。淬火回火后组织中有残留奥氏体存在时,KIC值也会提高。等温淬火球墨铸铁硬度值50~55(HRC)时,KIC值只有600~700MPa·m1/2。但是提高等温处理温度后,KIC值提高。
石墨球比较圆整时,球化率对KIC值没有明显影响。但球化率较低时(例如60%~70%),则球化率的影响就比较显著了。石墨球径越小,在其他条件相同时,KIC值越高。在石墨球密集区,相邻球体间应力集中效应明显,而且球体周围的疲劳裂纹容易连接起来形成较大裂纹,将会使KIC值显著降低。从断裂韧度的角度来看,应尽量避免石墨球的不均匀分布。
石墨球数对KIC值的影响见图3-23。表明增加球数可提高球墨铸铁的KIC值。

图3-23 石墨球数对KIC值的影响
温度对球墨铸铁的KIC值有影响。在不同温度下,各种球墨铸铁的KIC值列于表3-7。
表3-7 各种温度下球墨铸铁的KIC值

①除另有说明外,试样化学成分:ω(C)=3.6%,ω(Si)=2.5%,ω(Ni)=0.38%,ω(Mo)=0.35%。
3.1.11 抗热疲劳强度
金属在某一温度区间反复进行加热-冷却,经过许多次热循环后,由于各个组成相之间或组成相内部不同组分之间热膨胀性质不同,导致晶格失稳、晶体损伤,组织遭到破坏,铸件受到损伤。这种损伤称为热疲劳损伤。汽车发动机排气歧管、刹车鼓、玻璃模具、钢锭模等都是常见的需要较高抗热疲劳性能的铸件。这些铸件常以抗热疲劳性能作为评价铸造质量和工作寿命的主要标准。
球墨铸铁热疲劳与其高温强度、球状石墨形态与数量、组成相热膨胀系数、加热和冷却温度以及温度变化速率、热循环温差、热导率、铸件应用时是否受到结构约束等一系列因素有关。进行合金化调整铸件显微组织(包括石墨与基体)、降低热膨胀系数也是改善球墨铸铁抗热疲劳性能的重要措施。
3.1.12 高温力学性能
温度升高金属晶体强度和晶界强度都要下降。热激活作用增强,在外力作用下,原子迁移所需能量降低,更具有方向性,塑性变形容易进行。也就是说,高温加强原子扩散运动,促进晶粒本身的形变过程及晶界的滑动及迁移过程,从而使金属力学性能发生变化。温度越高,外力作用时间越长,这种影响越显著。
另外,金属组织类型在高温下可能发生的变化也会影响材料力学性能。在室温下对金属有强化作用的因素(例如固溶强化,形变强化)在高温时都会降低它们的作用,或者失去强化作用。
金属材料的高温力学性能与铸件加热温度、零件所受应力大小、应力作用时间长短有关。高温强度包括短时高温强度、高温持久强度、蠕变极限。这些指标对高温下使用的铸件都是重要的。短时高温强度是指在高温下进行短时间拉伸试验得到的结果。球墨铸铁的拉伸强度、屈服强度一般是随温度提高而降低。拉伸强度、屈服强度、伸长率的变化则因基体不同而有差异。室温至760℃范围内伸长率都有先降低后提高的趋势。
温度对球墨铸铁高温短时拉伸强度、屈服强度和伸长率的影响见图3-24。

图3-24 温度对球墨铸铁高温力学性能的影响
标称力学性能不同的球墨铸铁在-50~450℃温度范围内的许用拉伸应力列于表3-8。
表3-8 标称力学性能不同的球墨铸铁在-50~450℃温度范围内的许用拉伸应力

球墨铸铁的弹性模量也随温度的提高而降低。基体类型不同的球墨铸铁弹性模量随温度变化的情况如图3-25所示。

图3-25 温度对钢和球墨铸铁弹性模量的影响
1—铁素体+珠光体;2—铁素体;3—钢
3.1.13 蠕变与持久强度
通常规定在某一规定温度下经过100000h加热,总蠕变量小于0.1%的许用应力作为金属在某温度下的持久强度。
金属在一定温度和应力长时间作用下发生缓慢塑性变形现象称为蠕变。蠕变极限是促使金属发生蠕变的强度指标。即在一定温度和规定时间内获得一定总变形量的应力值。持久强度是指金属在高温和应力长时间作用下的断裂抗力。金属的抗蠕变能力和持久强度对于在高于室温工作的球墨铸铁件都是重要的。
图3-26显示温度和时间对球墨铸铁持久强度的影响。珠光体球墨铸铁持久强度高于铁素体球墨铸铁,但是当工作温度达到650℃时,两种球墨铸铁的持久强度已很接近,这可能与粒状珠光体出现有关。有些产品需要添加合金元素提高抗蠕变能力。钼、硅、铝是比较有效的合金元素,钼细化珠光体,增加组织的稳定性,提高球墨铸铁高温强度,改善抗蠕变能力非常有效。

图3-26 温度和时间对球墨铸铁持久强度的影响
3.1.14 高硅铁素体耐热球墨铸铁
当前有两种常用于高温环境的球墨铸铁:高镍奥氏体球墨铸铁和高硅铁素体球墨铸铁。本书将在第10章全面介绍高镍奥氏体球墨铸铁,这里只介绍高硅铁素体球墨铸铁。
铸铁类合金在高温下工作,其组织和性能都会发生一些变化。这些变化主要表现在:铸件表面脱碳起皮、内部氧化、铸件重量和尺寸增加、被称为氧化和热生长;材料强度、蠕变极限和持久强度相应降低;热疲劳寿命缩短;热冲击抗力减弱。高温下性状变化除与石墨形态、分布、数量有关外,还受基体金属类型和组织形态的显著影响。
球墨铸铁的铁素体基体是含碳量很低的单相组织。在高温环境中,铁素体不像珠光体那样发生共析渗碳体分解。碳从基体内部析出可导致铸件出现热生长。研究结果显示,铁素体中溶入硅、铝等合金元素,能够有效提高共析转变温度,使铸件组织在较高温度范围内不发生相变,有助于消减球墨铸铁件的热生长。含硅量达到4%~5%的高硅耐热球墨铸铁,例如ω(Mo)=0.3%~0.7%,ω(Si)=4.5%~5.5%硅钼球墨铸铁高温下的力学性能得到显著改善、抗热冲击及热疲劳性能显著提高。适用于在较高温度环境(300~700℃)中使用的零件。当球墨铸铁含硅量增加到10%以上,铸件使用温度可达750~800℃,用于制造诸如锅炉预热器、煤粉喷嘴、烟道闸门一类零件。也适用于汽车发动机排气歧管等耐热疲劳铸件。又能有效抵抗酸类腐蚀,成为优良的耐蚀铸铁。
耐热铸铁国家标准(GB/T9437)中列有4种硅系耐热球墨铸铁,化学成分、室温拉伸强度、硬度指标列于表3-9。
表3-9 硅系耐热球墨铸铁牌号、化学成分、室温拉伸强度和硬度指标

在高温环境中,硅系耐热铁素体球墨铸铁中硅受到氧化后,在铸件表面生成一层由FeO和SiO2组成的复合化合物(2FeO·SiO2),构成致密的、与铸件表面牢固结合的保护膜,保护膜阻止氧离子通过铸件表层向内部渗入,能够有效地减轻铸件氧化。
图3-27显示含硅量对球墨铸铁氧化物生成量以及共析转变温度的影响。由图可见,含硅量超过3.5%~4.0%时,抑制氧化的效果就比较稳定而显著了。

图3-27 含硅量对球墨铸铁氧化物生成量的影响(试样在空气中加热,保温100h)
1—700℃;2—850℃;3—加热时共析转变温度
800℃保温时,几种铸铁氧化增重率与硅系耐热铁素体球墨铸铁的比较示于图3-28。可以看出,硅系耐热铁素体球墨铸铁氧化增重率显著低于其他铸铁。

图3-28 几种铸铁800℃时氧化增重率与硅铁素体球墨铸铁比较
1—高碳灰铸铁;2—灰铸铁;3—铬耐热铸铁RTCr2;4—以蠕虫石墨为主的蠕墨铸铁;5—团状蠕虫石墨铸铁;6—中硅铁素体球墨铸铁;7—中硅蠕墨铸铁
硅系铁素体球墨铸铁室温力学性能并不随含硅量而发生相应变化。这是因为硅固溶于铁素体以及元素偏析或铁素体组织出现有序化,导致铁素体脆化所致。
硅系耐热球墨铸铁在600℃、700℃及800℃的抗拉强度和延伸率见表3-10。
表3-10 硅系耐热球墨铸铁高温力学性能

在高硅铁素体耐热球墨铸铁中硅能有效地降低球墨铸铁蠕变速率,提高持久强度,延长铸件工作寿命,但铸件含硅量达到4%左右效果才比较明显。球墨铸铁件同时添加钼和硅能产生更优良抗蠕变能力。铝、铬、硼、镍、铜也能提高球墨铸铁抗蠕变能力。铝的加入量在3.5~4.0之间效果较好。但铝也影响球墨铸铁的其他性能,使用时宜慎重。
另外,这种球墨铸铁还有很好的蠕变极限强度和热疲劳抗力。尤其是在材料中添加钼以后,效果更为显著。例如,采用ω(Si)=3.8%~5.0%、ω(Mo)=0.5%~1.2%硅钼球墨铸铁制造在200~850℃交变温度下工作的铸件,长期使用结果令人满意。适合制造汽车发动机排气歧管、涡轮增压器壳体等需要具有优良抗热疲劳性能的铸件。尺寸稳定性要求高的精密零件加钼量1.0%~1.5%时可取得很好的效果。
钼对ω(Si)=4%耐热球墨铸铁600℃蠕变应力的影响示于图3-29。表明加钼超过1%可以产生显著效果。

图3-29 加钼提高硅耐热球墨铸铁蠕变抗力
在硅系耐热球墨铸铁中加入钒,ω(V)<0.5%,材料在450~650℃之间的抗拉强度、屈服强度均有提高,其效果与加入同等数量钼的效果很接近。
3.1.15 低温力学性能
球墨铸铁的低温力学性能是近些年来铸造界许多人关注的问题。因为需要在低温(-200~-20℃)环境中承受重负荷的高韧性球墨铸铁件需要量越来越多。这些铸件常常处于设备的关键位置,例如装设在高寒地区的风力发电机箱体、铺设在高寒地区铁路钢轨下面的垫板等都在远低于0℃温度下使用。低温会使球墨铸铁的室温力学性能发生变化,可能使那些在室温下安全运行的零件在冬季突然损坏,为了确保设备安全运行。有必要探讨球墨铸铁的低温力学性能,保证设备能在低温环境中安全运行。
低温环境应用的铸件采用铁素体球墨铸铁。图3-30(a)显示铁素体球墨铸铁的几项基本力学性能指标随温度而变化的情况。图中几条曲线说明:随着材料温度的降低,铁素体球墨铸铁的抗拉强度、屈服强度相应提高,而其断后伸长率在低于一定温度时基本上没有大的变化,但在降低到某一温度界限后,延伸率开始急剧下降。说明材料在低温下逐渐由韧性向脆性转变。当材料受力达到屈服强度后,很小的变形就可能使零件发生断裂。

图3-30 球墨铸铁低温拉伸性能
铁素体球墨铸铁的低温冲击韧度高于珠光体球墨铸铁。图3-31表示几种球墨铸铁在不同温度下的冲击韧度。在韧-脆性转变温度方面。铁素体球墨铸铁的韧-脆性转变温度约在-50℃左右,而珠光体球墨铸铁的韧-脆性转变温度约在-20~20℃之间。基体中出现碳化物,特别是存在网状碳化物时,低温冲击值明显下降。

图3-31 几种球墨铸铁的韧-脆性转变温度
1—铁素体;2—铁素体+珠光体;3—粒状珠光体;4—珠光体
低温球墨铸铁的化学成分对铸件可靠性有影响。铁素体含硅量过分提高时,低温冲击值显著下降,韧-脆性转变温度显著增高。综合考虑硅对铁素体生成和低温冲击韧度的影响,硅质量分数保持在1.8%~2.0%较为合适。磷对低温冲击韧度也有较大影响。有资料报道,当磷的质量分数从0.057%增加到0.11%时,球墨铸铁韧-脆性转变温度由-40℃上升到接近室温。为了设备运行的安全性,低温使用的铁素体球墨铸铁件中磷含量都应控制在0.02%以下。锰和磷有相似的作用。为了避免产生晶间碳化物,改善材料在低温下的塑韧性,含锰量不要超过0.15%。
铁素体球墨铸铁缺口试样的低温冲击值远小于无缺口试样,缺口试样的韧-脆性转变温度接近室温。低温应用的铁素体球墨铸铁件切削加工时要特别注意避免出现尖锐缺口。
镍锰奥氏体球墨铸铁的低温韧性优于其他基体的球墨铸铁,在高寒地区可应用于重要铸件。
除此之外,应该设法细化铁素体球墨铸铁件晶粒。铸件晶粒尺寸减小可提高孪生屈服应力。晶粒细化到一定程度后,晶粒优先发生滑移变形,可以改善球墨铸铁的低温力学性能。