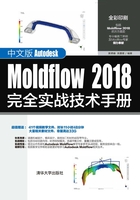
1.4 Moldflow有限元分析基础
Moldflow作为成功的注塑产品成型仿真及分析软件,采用的基本思想也是工程领域中最为常用的有限元法。有限元法的应用领域从最初的离散弹性系统发展到后来进入连续介质力学中,目前广泛应用于工程结构强度、热传导、电磁场、流体力学等领域。经过多年的发展,现代的有限元法几乎可以用来求解所有的连续介质和场问题,包括静力问题和与时间有关的变化问题以及振动问题。
简单说来,有限元法就是利用假想的线或面将连续的介质的内部和边界分割成有限个大小的、有限数目的、离散的单元来研究。这样就把原来一个连续的整体简化成有限个单元体系,从而得到真实结构的近似模型,最终的数值计算就是在这个离散化的模型上进行的。直观上,物体被划分成网格状,在Moldflow中将这些单元称为网格(mesh),如图1-6所示。

图1-6
1.有限元法的基本思想
有限元法的基本思想包括以下几个方面。
(1)连续系统(包括杆系、连续体、连续介质)被假想地分割成数目有限的单元,单元之间只在数目有限的节点处相互连接,构成一个单元集合体来代替原来的连续系统,在节点上引进等效载荷(或边界条件),代替实际作用于系统上的外载荷。
(2)由分块近似的思想,对每个单元按一定的规则建立求解未知量与接点相互之间的关系。
(3)把所有单元的这种特性关系按一定的条件(变形协调条件、连续条件或变分原理及能量原理)集合起来,引入边界条件,构成一组以接点变量(位移、温度、电压等)为未知量的代数方程组,求解它们就得到有限个接点处的待求变量。
所以,有限元法实质上是把具有无限个自由度的连续系统理想换为具有有限个自由度的单元集合体,使问题转换为适合于数值求解的结构型问题。
2.有限元法的特点
有限元方法正是由于它的诸多特点,在当今各个领域都得到了广泛应用。表现如下:
(1)原理清楚,概念明确;
(2)应用范围广泛,适应性强;
(3)有利于计算机应用。
3.Moldflow分析流程
对于常规的塑件,Moldflow 2018的一般分析流程如图1-7所示。
它包括三个主要的分析步骤:建立网格模型、设定分析参数、模拟分析结果。其中,建立网格模型和设定分析参数都属于前处理的范围,模拟分析结果为后处理。
(1)建立网格模型。
建立网格模型包括新建工程项目,导入或新建CAD模型,网格的划分、检查以及修复。导入或新建CAD模型时,通常根据分析的具体要求,对模型进行一定的简化。
(2)设定分析参数。
设定分析参数包括选择分析类型、成型材料、工艺参数。
参数设置中首先要确定分析的类型,确定主要的分析目的,选择相应的模块进行分析,然后在材料库选择成型材料,或自行设定材料的各种物理参数。按照注射成型的各种不同阶段,设置相应的温度、压力以及时间等各种工艺参数。
(3)模拟分析结果。
分析完成以后,就可以进行模拟分析计算了。
根据模型的大小,网格质量,分析类型的不同,分析时间的长短。在分析结束后,可以看到塑件成型后的各种信息。

图1-7
4.注塑成型模拟技术
注塑成型模拟技术是一种专业化的有限元分析技术,它可以模拟热塑性塑料注射成型过程中的充填、浇口和型腔中的流动过程,计算浇注系统及型腔的压力场、温度场、速度场、剪切应变速率场和剪切应力场的分布,从而可以优化浇口数目、浇口位置和注塑成型工艺参数,预测所需的注射压力和锁模力,并发现可能出现的短射、烧焦、不合理的熔接痕位置和气穴等缺陷。
作为行业的主导和先驱者,Moldflow的注塑成型模拟技术也经历了中性面模型、表面模型和三维实体模型3个发展阶段。
(1)中性面模型技术。
中性面模型技术是最早出现的注塑成型模拟技术,其采用的工程数值计算方法主要包括基于中性面模型的有限元法、有限差分法和控制体积法等。其大致的模拟过程如图1-8所示。

图1-8
中性面模型技术具有以下优点。
① 技术原理简明,容易理解;
② 网格划分结果简单,单元数量少;
③ 计算量较小,即算即得。
但中性面模型技术仅考虑产品厚度小于流动方向的尺寸,塑料熔体的黏度较大,将熔体的充模流动视为扩展层流,忽略了熔体在厚度方向的速度分量,因此所分析的结果是有限的、不完整的。
(2)表面(双层面)模型技术。
表面模型技术是指型腔或制品在厚度方向上分成两部分。与中性面模型不同,它不是在中性面,而是在型腔或制品表面产生有限网格,利用表面上的平面三角网格进行有限元分析。
相应地,与基于中性面的有限差分法在中性面两侧进行不同,厚度方向上的有限差分仅在表面内侧进行。在流动过程中,上下两表面的塑料熔体同时并且协调地流动,其模拟过程如图1-9所示。
Moldflow的Fusion模块采用的就是表面(双层面)模型技术,它基于Moldflow的独家专利Dualdomain分析技术使用户可以直接进行薄壁实体模型分析。
虽然从中性面模型技术跨入表面模型技术,可以说是一个巨大进步,也得到用户的好评,但是,表面模型技术仍然存在一些缺点:
① 分析数据不完整;
② 无法准确解决复杂问题;
③ 缺乏真实感。

图1-9
(3)实体模型技术。
Moldflow的Flow3D和Cool3D等模块通过使用经过验证的、基于四面体的有限元体积网格解决方案技术,可以对厚壁产品和厚度变化较大的产品进行真实的三维模型分析。
实体模型技术在数值分析方法上与中性面流技术有较大变化。在实体模型技术中熔体在厚度方向上的速度分量不再被忽略,熔体的压力随厚度方向变化。其模拟过程如图1-10所示。

图1-10
与中性面模型或表面模型相比,由于实体模型考虑了桶体在厚度方向上的速度分量,所以其控制方才要复杂得多,相应的求解过程也复杂得多,计算量大,计算时间长,这是基于实体模型的注塑流动分析目前所存在的最大问题。