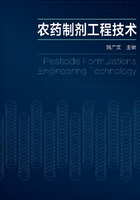
第四节 气流粉碎设备
一、简述
1. 气流粉碎简述
气流粉碎机也称气流磨,自1882年戈斯林首先提出利用气流动能进行粉碎以来,到现在已有一百多年的历史,是一种比较成熟的技术。它利用高速气流(300~500m/s)或过热蒸汽(300~400℃)的能量使颗粒产生强烈多相紊流场,固体颗粒相互产生冲击、碰撞或摩擦作用,致使颗粒被粉碎。
气流粉碎机一般按气流的作用分类、按流体介质种类分类、按给料方式分类、按颗粒加速方式分类或按分级特性分类等。目前,气流粉碎机使用最多的是扁平式、循环管式、对喷式、靶式、对喷流化床式五种类型。
由于气流粉碎不受物料物性的影响,在粉碎过程中不产生热量,所以适合热敏性物料的粉碎。工作介质可以是空气、稀有气体。同时在粉碎中几乎没有机械零部件磨损、没有杂质渗入,从而保证了产品的质量。而且能耗低、生产量大、制造简单、操作简便,且粉碎细度能达到0.1μm以下,因而,气流粉碎越来越受到人们的重视。
为了提高我国农药的加工水平,加速提高粉体农药的质量,在20世纪80年代末到90年代初,气流粉碎技术开始在大型国有农药企业应用。但是当时因传统观念以及资金等问题,该技术并没有得到广泛应用,绝大部分的农药企业依然采用传统的落后的加工技术。随着经济的发展,直到20世纪90年代末期,农药企业开始逐步采用气流粉碎技术。
农药超细粉碎不仅可以大幅提高农药有效体含量和用药效果,减少施药量,而且还可以使农药更快地在作物内部代谢,加速农药使用后的降解,大大降低农药在作物表面及内部的残留。因此,超细粉碎更是保障农药使用安全和环保的需要,所以气流粉碎机目前在我国的农药超细粉碎中广泛使用。从第一代的水平圆盘气流粉碎机到第二代“O”形管气流粉碎机,再到目前的第三代流化床气流粉碎机,现在已成为农药超细粉碎的主流机型。
2. 气流粉碎原理
气流粉碎机是利用高速旋转气流的能量来加速被粉碎的粒子。通过粒子之间的高速冲击摩擦以及气流分子对物料粒子的剪切作用而将粒子粉碎至10µm以下。由于采用压缩空气为动力,故气体在喷嘴处膨胀时,能够吸收由于粉碎而产生的热量,有效降低了粉碎的环境温度,使物料在粉碎过程中不升温。所以气流碎粉机可以粉碎较低熔点的物料。在农药剂型加工中气流粉碎机主要用来将低熔点原药加工成高浓度母粉、高浓度可湿性粉剂和水分散粒剂的基料。
3. 气流超细粉碎在农药加工中的作用
气流超细粉碎在农药生产中的应用越来越广泛,特别是近年来,农药超细粉碎在细度要求和应用种类上都呈大幅上升趋势。随着农药加工技术的发展,农药生产中对超细粉碎的要求将会越来越普遍,农药原药、可湿性粉剂大都有超细化的要求。气流超细粉碎已经成为提高现代农药生产工艺和产品质量的最佳选择。农药超细化粉碎的工艺已经成熟,但是在超细化粉碎生产过程中,设备配置的合理性、卫生、安全与环保已经成为超细粉碎加工的关键环节。
由于环境的要求,农药正朝着超高效、毒性低、低用量的方向发展。每亩用药量为几克,甚至不到1g的产品已不断出现。通常要将药粒粉碎到微米级,所以气流粉碎机目前在我国农药可湿性粉剂和水分散粒剂原料的加工中广泛使用。从第一代的扁平圆盘式气流粉碎机,发展到第二代循环管式气流粉碎机和第三代对喷式流化床气流粉碎机。对一些产品的试验表明:在相同的能耗下,对喷式流化床气流粉碎机比扁平式气流粉碎机生产效率高,且粒度分布也比后者均匀。
4. 气流粉碎机的应用
在农药行业中,所需要粉碎的物料大致有原药干粉、可湿性粉剂、农药填充剂、农药助剂、水分散粒剂等几大类。
(1)原药干粉 经过气流超细粉碎机粉碎的原药干粉,可以大幅度提高原药的使用效果。一般原药的干粉粉碎到600目以上,既可以大幅提高原药的活性,也可以改善农药的使用效果,使农药更快更好地发挥作用,还可以大幅提高原药的利用率。
(2)可湿性粉剂 可湿性粉剂经过超细粉碎,可以大幅度提高悬浮率。一般粉碎到600目左右后,就可以达到70%以上的悬浮率,大幅改善农药的使用效果。
(3)农药填充剂 农药填充剂有很多种,主要有高岭土、白炭黑、凹凸棒、膨润土等。农药填充物经超细粉碎至600目以上,可以改善农药与各成分之间的混合效果,避免产生偏析现象,在水中不易沉淀,使农药具有更好的分散性,使各成分能够更加均匀地分布。
(4)农药助剂 经超细粉碎的农药助剂,可以大幅度增加比表面积,使助剂能够均匀地吸附于活性成分表面,充分发挥表面活性剂(农药加工助剂多为表面活性剂)的作用,也可以提高助剂的使用效率。一般农药助剂的使用要求为800目以上即可(固体剂型)。
(5)水分散粒剂 在加工水分散粒剂之前,一般将原药、填料、助剂等材料按一定比例混合均匀后进行气流粉碎,粒度为5~15μm。加工成类似可湿性粉剂的剂型后再进行造粒,产品悬浮率可以达到70%以上。
二、扁平式气流粉碎机
扁平式气流粉碎机的应用较早,可以称得上是第一代气流粉碎机。其结构如图1-17所示,工作原理如图1-18所示。主要由气流分配室、粉碎分级室、气流喷嘴、喷射式加料器、产品收集器等部件组成。分配室与粉碎分级室相通,高速气流经入口首先进入气流分配室在环向均匀分布,由于气流有很高的压力,从分配室强行通过喷嘴进入粉碎分级室。气流通过喷嘴时产生每秒几百米甚至近千米的高速,物料受到气流强大冲击力的作用,相互摩擦、碰撞发生粉碎。由于喷嘴与粉碎分级室成一定角度,气流夹带被粉碎物料做水平圆周运动。粉碎合格的产品进入中心处,经分离出料。由于结构的限制,此机型不宜进行大规模生产。另外,粉碎有黏附性的物料有时会有黏壁的倾向,必要时可以加入少量隔离剂如滑石粉等以防黏壁和黏附分级叶轮。表1-1列出了扁平式气流粉碎机的主要技术参数。

图1-17 扁平式气流粉碎机结构简图

图1-18 扁平式气流粉碎机工作原理图
1—粉碎带;2—粉碎喷嘴;3—文丘里喷嘴;4—推料喷嘴;5—垫片;6—外壳
表1-1 扁平式气流粉碎机的主要技术参数

注:空气压力0.6~0.70MPa。
扁平气流粉碎机有如下特点:
① 适用于干式超微工艺。由于冲击速度高,可达2.5马赫(1马赫=340.3m/s)以上,一般情况下很容易获得1~10μm粒子,根据物料性质,还能得到小于1μm的粒子。
② 由于粉碎机内部有闭路分级机构,制品中粗粒子不断循环粉碎,因而能获得粒度均匀、分布范围窄的制品。
③ 该设备具有粉碎时间短、结构简单、操作检修方便、占地面积小、低噪声(小于72dB)和无振动等优点。
④ 粉碎效率高,能进行连续粉碎,能保持粉碎制品纯度。
图1-19为扁平气流粉碎机的三维图。

图1-19 扁平气流粉碎机三维图
三、喷射粉碎机
喷射粉碎机工作原理如图1-20所示。通过装设在粉碎室内的喷嘴把压缩空气或高压蒸汽的能量转变成动能,形成高速气流轨迹,在这种超声速喷射气流中连续而且自动地供给粉粒体物料,让物料之间产生强烈的冲击和摩擦,从而进行粉碎。根据计算的喷嘴角度所产生的旋转涡流,不仅达到了粉碎的目的,而且由于离心力的作用还能达到分级的目的,可使超微粒子被分离出来。另外,从喷嘴喷射出来的空气通过绝热膨胀的作用使温度下降,因而能够进行低温粉碎,如图1-20所示。被粉碎的原料通过喷射器6被送到粉碎室里,从喷射器6处喷射进去的压缩气体通过喷射环2喷射到粉碎室里。这时,由于产生的喷射气流4的作用,原料便被粉碎成超微粒子。被粉碎的物料从排料口7与膨胀了的空气一起被排放出来。

图1-20 喷射粉碎机工作原理
1—压缩空气进口;2—喷射环;3—气流;4—喷射气流;5—加料口;6—喷射器;7—排料口
粉碎后产品可用旋风分离器、布袋除尘器等进行收集。原料的供给装置可使用振动加料器或螺旋送料器,喷射粉碎系统流程如图1-21所示。

图1-21 喷射粉碎机流程图
1—空气压缩机;2—二次冷却器;3—空气罐;4—空气干燥器;5—喷射粉碎机;6—加料器;7—除尘器
粉碎后的粒子直径通过调节投入量的办法就能简单地进行控制。在粉碎室中由于经常滞留有很多物料,因此,这些物料就起到了制动作用,使粉碎室内涡流旋转方向上的分速度减小。物料的投入和排出正好保持着均衡的比例,喷射粉碎机各型号的主要技术参数如表1-2所示。
表1-2 喷射粉碎机技术参数

四、立式循环管气流粉碎机
立式循环管气流粉碎机是继扁平式气流粉碎机之后开发出的一种机型,可以认为是第二代气流粉碎机,外形如图1-22所示。粉碎室为立式环形结构,下部为粉碎区,上部为分级区。在粉碎区安装若干个喷嘴,各喷嘴安装位置应使喷出气流的轴线与粉碎室中心线相切。物料经加料器定量进入粉碎区,压缩空气或过饱和蒸汽经过喷嘴进入粉碎室,将物料颗粒加速。物料颗粒之间产生冲击碰撞,气流夹带被粉碎物料沿循环管向上运动,进入分级区。由于离心力场的形成使密集的颗粒流分离,大颗粒在外层,细小颗粒在内层。物料出口设在循环管的内侧,在出口处安装百叶窗式惯性分级器,使细颗粒通过分级器时又进行一次分离。粗大颗粒弹回粉碎室继续粉碎,细颗粒排出机外通过旋风分离器收集。

图1-22 立式循环管气流粉碎机
1—出料口;2—导叶;3—进料口;4—粉碎机;5—加料喷嘴;6—文丘里喷嘴;7—粉碎喷嘴
物料经加料器由文丘里喷嘴送入粉碎区,气流经一组粉碎喷嘴喷入不等径变曲率的循环管式粉碎室并加速颗粒,使之相互冲击、碰撞、摩擦而粉碎。气流旋流携带出被粉碎的颗粒,沿上行管向上运动进入分级区。在分级区,由于离心力场的作用与分级区壳体的配合,密集的颗粒流分流。细粒在内层经分级器分级排出作为成品捕集,粗粒在外层沿下行管返回继续循环粉碎。
该循环管式粉碎室内腔截面不是真正的圆截面,循环管各处的截面也不相等。分级区和粉碎区的弧形部分也不是圆周的一部分,即曲率半径是变化的。由于循环管的这种特殊形状设计,其具有加速颗粒运动和加大离心力场的功能,提高了粉碎和分级效果。此外,由于分级区的弯曲管壁设计成减摩曲线状,所以循环管内壁的磨损大大减轻。
立式循环管气流粉碎机的粉碎粒度可达0.2~3μm,广泛应用于农药以及具有热敏性和爆炸性的化学品等的超细粉碎。
粉碎、分级流程如图1-23所示,空气经压缩机压缩经粗滤器15、干燥器16、油分离器17进入压缩空气缓冲罐,干净的压缩空气分别进入粉碎机的加料喷嘴和粉碎喷嘴,加入物料进行粉碎。被粉碎的物料与气流一起进入分离器,粗粉粒经回转阀与原料一起回粉碎机进行粉碎。符合要求的微粉与气流一起进入旋风分离器进行分离,由回转阀9收集成品微粉。更小的微粉与气流一起进入布袋除尘器10进一步分离,由回转阀11收集超微粉成品,而废气由排风机12排出。表1-3是国产循环管式气流粉碎机的主要技术参数。

图1-23 粉碎、分级流程图
1—原料斗;2—加料器;3—喷射粉碎机;4—分离器;5,9,11—回转阀;6—旋流器;7—打落器;8—成器仓; 10—布袋除尘器;12—排风机;13—消声器;14—空压机;15—粗滤器;16—干燥器;17—油分离器
表1-3 循环管式气流粉碎机主要技术参数

注:空气压力0.65~0.70MPa。
五、对冲式气流粉碎机
图1-24是对冲式气流粉碎机的结构示意图。这种粉碎机问世很晚(1956),为美国Trost Mill公司所发明。它的粉碎部分采用逆向气流粉碎机结构,分级部分则采用扁平式气流粉碎机结构,因此兼有两者的特点,是一种先进的气流粉碎机。内衬和喷嘴的更换方便,与物料和气流相接触的零部件可用聚氨酯、碳化钨、陶瓷、各种不锈钢等耐磨材料制造。

图1-24 对冲式气流粉碎机结构示意图
1—微粉的运动轨迹;2—通风口;3—粗粒的运动轨迹;4—上升通道;5—原料供给料斗;6—压缩空气;7—粉碎区;8—压缩空气;9—返回通道;10—分级区
该气流粉碎机的工作过程:由料斗喂入的物料被喷嘴喷出的高速气流送入粉碎室,随气流上升至分级室,在此气流形成主旋流使颗粒分级。粗颗粒排至分级室外围,在气流带动下返回粉碎室再进行粉碎,细颗粒经产品出口排出机外捕集为成品。
对冲式气流粉碎机的粉碎室相对安装两个喷管。喷嘴喷入高速气流将物料吹入喷管,使其在管内加速。加速后的物料随同气流离开喷管,与对面喷管喷出的气流形成对冲,达到粉碎目的。粉碎后的细粉随同气流进入静态分级器,细粒在分级器中央排出;粗粒则由于离心力作用下落至对面的喷嘴处,并被喷出的气流在喷管内加速,重新粉碎,该粉碎机的处理量为10~500kg/h。
六、对撞式气流粉碎机
对撞式气流粉碎机为两束载物气流在粉碎室中心正面碰撞,颗粒在气流高速冲击下互相碰撞瞬间粉碎,见图1-25。随后,粗细粒子在气流带动下向上运动,进入与其串联的分级机。由于分级转子高速旋转,分级粒径以下的细粒子通过分级器中心排出,进入与之相连的旋风分离器、脉冲除尘器中进行捕集。分级粒径以上的粗粒子受离心力作用,沿内壁向下运动,返回对撞式气流粉碎机,再次在磨腔中央与给料射流相撞,从而再次粉碎。如此周而复始,直至达到产品粒度要求为止,图1-26是该机的工艺流程。

图1-25 对撞式气流粉碎机工作原理图

图1-26 对撞式气流粉碎机工艺流程
1—空气压缩机;2—储气罐;3—除油器;4—冷冻干燥机;5—过滤器;6—对撞式 气流粉碎机;7—分级机;8—旋风分离器;9—布袋除尘器;10—引风机
七、对喷流化床式气流粉碎机
1. 对喷流化床式气流粉碎机简述
20世纪70年代初,德国Alpine公司成功开发了对喷流化床式气流粉碎机。
对喷流化床式气流粉碎机以高压气体为动力,据介绍,它比其他冲击式粉碎机可以节能50%以上。由于不需像机械粉碎那样金属部件承受巨大的冲击力,产品中少有金属粉末混入,可以保证产品的纯度,是农药干式粉碎的理想设备。该设备工作噪声低,一般低于80dB,可以处理莫氏硬度在10以上的物料。产品细度有97%在2~200µm,而且具有设备体积小、维修费用低等优点。是目前农药干粉碎的主力机型。
粉碎室是一个立式圆柱形结构,高压气流喷嘴在粉碎室底部沿周向对称布置,以利于气流的平衡。产品出口布置在粉碎室上部,出口处有一个或多个分级器,见图1-27。分级器有多种规格,根据产品要求可以选择金属和非金属材料。物料经加料口进入粉碎室并向下落,当物料落入粉碎区时,被强大的气流冲击,物料受到冲撞、剪切等作用被粉碎。粉碎后物料受气流夹带向上运动,经分级器排出粉碎机并与气体分离,大颗粒被截留进一步粉碎。在这里,分级器起到切割产品粒径的作用,从而保证了产品的粒度分布。

图1-27 对喷流化床气流粉碎机外形
1—分级器电机;2—加料口;3—粉碎室;4—压缩空气管;5—粉碎喷嘴;6—机架;7—排渣口;8—分级器
2. 对喷流化床气流粉碎机的优越性
对喷流化床气流粉碎机与其他机械方法粉碎相比有着非常明显的优越性。在整个粉碎过程中没有机械磨损,而是依靠物料颗粒自身撞击达到粉碎。这种粉碎方式有以下几大优点:①粉碎过程中是空气带动物料在运行,所以不会升温,对于各种物料不会造成任何不良影响;②粉碎过程没有直接的机械摩擦,不使用任何固体的研磨介质,因此不会有任何杂质掺入物料之中,可以绝对保障物料的纯度;③对喷流化床气流粉碎的细度可以随产品需求而自由调节;④生产过程始终是连续的,不管是要求什么细度,加料和出料都不需要人为间隔和停顿,都是由其控制系统自动控制进料和出成品的速率;⑤整个系统是负压操作,在粉碎过程中不会有扬尘等现象,可以很好地控制现场卫生、安全和环境。
气流粉碎也存在能耗和投资成本相对高的缺点,针对能耗高的问题,需要农药厂家在上新项目的时候多关注产能及成本,对于附加值和要求不高的产品可以考虑用其他类型的粉碎设备,但是在农药行业一般农药不存在这样的问题,因为农药一般要求粉碎细度在600~800目,所以能耗是完全可以接受的。
3. 对喷流化床气流粉碎机的原理
对喷流化床气流粉碎机主要是利用超声速气流带动物料颗粒相互撞击而达到粉碎的效果。对喷流化床气流粉碎机由加料口、粉碎室、出料口、分离室等组成。物料通过螺旋加料器进入粉碎室、压缩空气通过粉碎喷嘴向粉碎室高速喷射。物料在超声速喷射气流中加速,并在喷射气流交汇处反复冲击、碰撞,达到粉碎。被粉碎物随上升气流到达分级室,由于分级叶轮高速旋转,物料颗粒受到高速旋转的分级叶轮产生的向心力和离心力作用,达到粉碎要求的在分级粒径以下的颗粒受到的向心力大于离心力,在负压气流吸引下进入分级叶轮内部并到达出料口。大于分级要求的颗粒受到的分级叶轮产生的离心力大于向心力,不会受负压气流的吸引而落回到粉碎室继续进行冲击粉碎。如此往复,使物料达到理想的粉碎效果。从出料口排出的成品随气流进入旋风分离器、脉冲除尘器(捕集器)收集,气体由引风机排出。图1-28是对喷流化床式气流粉碎机工作原理示意图。

图1-28 对喷流化床气流粉碎机工作原理
1—加料口;2—粉碎室;3—出料口;4—分离室
4. 产品粒度的控制
分级轮与出料管之间合理的气密封设计,保证粗颗粒不会混入成品中。轴承结构及轴承座的气流密封、气流冷却,使轴承在常温下正常工作,保证了轴承长期使用及机械运行平稳性。
流化床气流粉碎机粉碎不同物料时,主机内部的物料浓度也不同,为保证主机在最佳工况下工作,发挥最佳的工作效率,自动加料机与主机之间采用智能机电一体化控制原理,根据主机内部物料浓度来控制加料速度,确保主机在设定的最佳浓度下工作,控制原理见图1-29。

图1-29 控制原理框图
5. 生产中的安全、卫生和环境控制
流化床气流粉碎机在农药生产中的卫生、安全和环境控制方面与其他粉碎方式相比具有明显的优越性。
流化床气流粉碎机的全系统是负压,生产现场不会造成扬尘,同时,最后排放的空气是经过布袋除尘器过滤的洁净空气(过滤精度为0.1μm)。因此,整个系统不会带来任何环境影响。
适用于农药生产的流化床超细粉碎系统,从加原料、加助剂、混合、出成品至自动包装都实现了全自动化控制,生产现场实现了无人化作业。在系统设置方面,充分考虑了农药生产的特点,原料加料前设有自动加料装置和混合设备。原料进入粉碎主机实行自动控制加料,成品出料后也设有自动加料装置和混合设备,成品出口设有全自动包装机。可以保障生产现场的卫生、安全和环保要求,避免在农药超细化生产中对人员造成伤害。
在选择产品的时候,气流粉碎机的产量和能耗比是重点考虑的要素。气流粉碎机从上述的原理来看是比较简单的,但是每种产品都有自己的关键部分。分级轮和喷嘴的精度决定着气流粉碎机的性能。
流化床气流粉碎系统已经广泛应用于各类农药的超细粉碎生产。主要有除草剂、杀虫剂、杀菌剂等品种的超细粉碎。
6. 流化床气流粉碎生产实例
简易工艺流程如图1-30所示,粉碎主机气源由压缩机、储气罐、除油器、过滤器、冷冻干燥机等组成的气流系统提供,粉碎所需工作压力一般在0.7MPa以上。成品粉体通过旋风分离器、布袋除尘器收集。洁净的空气由引风机排出。部分农药粉碎指标如下:
每小时耗电130kW·h;
40%硫黄:原料100目,成品d97<10μm,产量800kg;
多菌灵:原料100目,成品悬浮率92%~93%,产量1500kg;
70%代森锰锌:原料100目,成品d97<5μm,产量1000kg。

图1-30 流化床气流粉碎机简易工艺流程
对于一般需要混合的干粉农药、可湿性粉剂一般采用气流粉碎混合系统。根据农药生产的需要,可以有多种流程布置。图1-31为间歇式生产方式,适用于小规模生产或经常更换品种的情况。图1-32适用于大规模生产,是连续化的生产方式。

图1-31 间歇式生产流程

图1-32 连续型、适用于大量生产流程
部分机型粉碎农药的工艺参数见表1-4。
表1-4 农药的工艺参数

八、闭路循环系统
农药在超细粉碎状态下,对人身的毒副作用将成倍增加,不仅口鼻是其进入人体的通道,皮肤毛孔都会成为其侵害人体的部位。因此,对于低毒性的农药,也需要使用全封闭的自动化系统进行超细粉碎。对于一些粉尘泄漏对人体有害或者可能发生爆炸的物料,采用的是闭路循环系统,以达到环保和安全的要求。基本流程见图1-33。

图1-33 惰性气体保护气流粉碎系统基本流程
惰性气体保护气流粉碎系统特点:
① 适用性强,根据易燃易爆物料的性质,可选择与其相适应的气体作为粉碎介质。
② 惰性气体循环使用,消耗极小。
③ 惰性气体中的氧气含量可控制在1μL/L左右,并且氧含量可任意设定。
④ 系统采用先进的触摸屏、可编程序PLC控制器,实现了全自动控制。