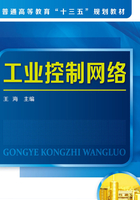
1.4 现场总线与信息化集成技术
1.4.1 现场总线
尽管近年工业控制网络的发展,出现如无线数传、借助移动公网很多种形式,但现场总线依然在控制网络中发挥主要角色。
国际电工委员会制定的国际标准IEC61158对现场总线(Fieldbus)的定义是:安装在制造或过程区域的现场装置与控制室内的自动控制装置之间的数字式、串行、多点通信的数据总线称为现场总线。
第2版(Ed2.0)IEC61158-2用于工业控制系统中的现场总线标准(第2部分)物理层规范(Physical Layer Specification)与服务定义(Server Definition)又进一步指出:现场总线是一种用于底层工业控制和测量设备,如变送器(transducers)、执行器(actuators)和本地控制器(local controllers)之间的数字式、串行、多点通信的数据总线。
在现场总线控制系统中,总线设备主要分为6类:变送器/传感器;网桥/网关/中继器/集线器/;交换机/路由器;执行器;控制器;监控/监视计算机;其他现场总线设备。
由于国家、公司等利益的原因,现场总线领域竞争激烈,某个品牌很难统一整个世界市场。IEC61158是制定时间最长、投票次数最多、意见分歧最大的国际标准之一。
但现场总线结构与功能高度分散,现场设备的互操作性与互换性好,协议相对公开,为企业信息系统的构建创造了重要条件,其信息集成的方式主要有:①在硬件上,采用专用网关完成不同通信协议的转换,把控制网段连接到基于以太网的管理网络;②在软件上,采用OPC等通用技术,将控制网络信息传送到管理网络,形成管控一体化网络。各种生产企业的MES、SIS、数字化企业等都是这种思路的集成系统。
本书将主要介绍Modbus、PROFIBUS-DP和AB公司的CIP控制网络及现场总线,将在后面详细阐述,这里对另外几种也较具影响力的现场总线简单介绍。
(1)基金会现场总线FF(Foundation FieldBus)
基金会现场总线FF前身是以美国Fisher-Rousemount 公司为首,联合Foxbora、横河、ABB、西门子等80 家公司制订的ISP 协议,以及Honeywell公司为首,联合欧洲等地的150家公司制订的WorldFIP协议。屈于用户的压力,这两大集团于1994 年9 月合并,成立了现场总线基金会,致力于开发出国际上统一的现场总线协议。
FF 以ISO 开放系统互联模型为基础,取物理层、数据链路层、应用层为FF通信模型的相应层次,并在应用层上增加了用户层。用户层主要针对自动化测控应用的需要,定义了信息存取的统一规则,采用设备描述语言规定了通用的功能块集。
FF 总线包括 FF通信协议、ISO 模型中的2~7层通信协议的通栈、用于描述设备特性及操作接口的DDL设备描述语言、设备描述字典,用于实现测量、控制、工程量转换的应用功能块,实现系统组态管理功能的系统软件技术以及构筑集成自动化系统、网络系统的系统集成技术。
FF 分为低速 H1和高速H2两种通信速率:H1通信速率为31.25kbps,通信距离可达1900m,支持总线供电;H2通信速率为1Mbps和2.5Mbps,通信距离为750m和500m。物理传输介质可支持双绞线、光缆和无线,采用曼彻斯特编码。
WorldFIP现场总线定义了物理层、数据链路层和应用层三层通信协议,结构相对简单。
在数据链路层,WorldFIP协议提供了变量及消息两种传输机制。
“变量”是指周期性地在网络上传输的数据包,每一个变量有一个唯一的16位数据标识,这种周期性报文根据预先设定的时间周期性地在网络上传输。在实际应用中通常被用于传输实时状态及控制信息,如控制现场I/O 实时状态、各种现场遥测值等。
“消息”主要用于传输一些诸如配置信息、诊断信息及事件信息等非周期性数据,消息只有在应用程序提出传输申请后一次性地在网络上传输。
WorldFIP中对传输介质的访问控制类似于“令牌网”。“令牌”是对介质的访问权,“令牌” 按照预先确定的时间在多个通信子站之间传递。“令牌”的传递过程由通信控制器自动完成,不需要应用程序的干预。
生产者/消费者模式:变量的生产者可以按照固定的时间间隔将变量在网络上广播,变量的消费者同时接收变量内容。在固定的时间窗内当所有通信子站生产的变量数据被发送后,“令牌” 被传递给提出发送消息请求的通信子站,此时得到“令牌”的通信子站将消息在网络上广播。
因此,WorldFIP非常适合于对于传输时间具有严格要求的场合,同时也使得某些突发数据能够尽快在网络上传输。
(2)CC-Link
CC-Link(Control &Communication Link)是三菱电机于1996 年推出的开放式现场总线,其数据容量大,通信速度多级可选择,而且它是一个复合的、开放的、适应性强的网络系统,能够适用于较高的管理层网络到较低的传感器层网络的不同范围。CC-Link是一个以设备层为主的网络,一般情况下,CC-Link整个一层网络可由1 个主站和64个从站组成。CC-Link具有高速的数据传输速度,最高可达10Mbps,其底层通信协议遵循RS-485。CC-Link的数据通信方式可分为2 种方式:循环通信和瞬时传送。
CC-Link系统是通过专用的通信模块和电缆将分散的I/O模块及特殊功能模块等设备连接起来,并通过PLC的CPU来控制和协调这些模块的工作。
网络中的主站由三菱FX系列以上的PLC或计算机担当,从站可以是远程I/O模块、特殊功能模块、带有CPU的PLC本地站、人机界面、变频器及各种测量仪表、阀门等现场设备,整个系统通过屏蔽双绞线连接。CC-Link具有性能卓越、应用广泛、使用简单、节省成本等突出优点。
① 组态简单 CC-Link不需要另外购买组态软件即可对每一个站进行编程。只需使用通用的PLC编程软件在主站程序中进行简单的参数设置,或者在具有组态功能的编程软件中设置相应的参数,便可以完成系统组态和数据刷新的设定工作。
② 接线简单 系统接线时,仅需使用3芯双绞线与设备的两根通信线DA、DB及接地线DG连接,并接好屏蔽线SLD和终端电阻,即可完成一般系统的接线。
③ 设置简单 系统需要对每一个站的站号、传输速率及相关信息进行设置,而CC-Link的每种兼容设备都有一块CC-Link接口卡,通过接口模块上相应的开关就可进行相关内容的设置,操作方便直观。
④ 维护简单、运行可靠 由于CC-Link的上述优点和丰富的RAS(Reliability, Availability, Serviceability)功能,使得CC-Link系统的维护更加方便,运行可靠性更高。其监视和自检测功能也使CC-Link的维护和故障后的恢复变得方便和简便。
系统具有备用主站功能、故障子站自动下线功能、站号重叠检查功能、在线更换功能、通信自动恢复功能、网络监视功能、网络诊断功能等,提供了一个可以信赖的网络系统,帮助用户在最短时间内恢复网络系统工作。
一个CC-Link系统必须有一个主站且只能有一个主站,主站负责控制整个网络的运行。但为防止主站出现故障而导致整个系统瘫痪,CC-Link可以设置备用主站,即当主站出现故障时,系统可自动切换到备用主站上。
CC-Link提供循环传输和瞬时传输两种通信方式,一般情况下,CC-Link主要采用循环传输的方式进行通信,即主站按照从站站号依次轮询从站,从站再给予响应。因而无论是主站访问从站还是从站响应主站,都是按照站号进行的,从而可避免由通信冲突造成的系统瘫痪;还可依靠可预见的、不变的I/O响应为系统设计者提供稳定的实时控制。对于整个网络而言,循环传输每次链接扫描的最大容量是2048位和512字,在循环传输数据量不够的情况下,CC-Link还能提供瞬时传输功能,将960字节的数据用专用指令传送给智能设备站或本地站,而且瞬时传输不影响循环传输的进行。
三菱常用的网络模块有CC-Link通信模块FX2N-16CCL-M、FX2N-32CCL,CC-Link/LT通信模块FX2N-64CL-M,CC-Link远程I/O链接模块FX2N-16Link-M和AS-i网络模块FX2N-32ASI-M等。
(3)CANopen
CANopen是一种架构在控制局域网路(Controller Area Network, CAN)上的高层通信协议,包括通信子协议及设备子协议,常在嵌入式系统中使用,也是工业控制常用到的一种现场总线。
CANopen 实现了OSI模型中的网络层以上(包括网络层)的协定。CANopen 标准包括寻址方案、数个小的通信子协定及由设备子协定所定义的应用层。 CANopen 支援网络管理、设备监控及节点间的通信,其中包括一个简易的传输层,可处理资料的分段传送及其组合。一般而言数据链接层及物理层会用CAN来实作。除了 CANopen 外,也有其他的通信协定(如EtherCAT)作 CANopen 的设备子协定。
(4)Lonwork
Lonwork是局部操作网络Local Operating Network的缩写,由美国Echelon公司于1992年推出,并由Motorola、Toshiba公司共同倡导,最初主要用于楼宇自动化,但很快发展到工业现场控制网。
Lonwork采用ISO/OSI模型的全部7层通信协议,并采用面向对象的设计方法,通过网络变量把网络通信设计简化为参数设置,最高通信速率为1.25Mbit/s,传输距离不超过130m;最远通信距离为2700m,传输速率为78kbit/s,节点总数可达32000个。
网络的传输介质可以是双绞线、同轴电缆、光纤、射频、红外线、电力线等多种通信介质,特别是电力线的使用,可将通信数据调制成载波信号或扩频信号,然后通过耦合器耦合到交流220V或其他交直流电力线上,甚至耦合到没有电力的双绞线上。电力线收发器提供了一种简单有效的方法将神经元节点加入到电力线中,这样就可以利用已有的电力线进行数据通信,大大减少通信中遇到的布线复杂等问题。这也是Lonwork技术在楼宇自动化中得到广泛应用的重要原因。
1.4.2 制造企业信息集成技术
实施制造企业信息化的关键是建立企业的信息化系统。信息化系统的内容包括管理信息系统和控制信息系统两大部分,具体在四个方面:①以CNC、PLC(DCS)、机器人等为核心的机电液一体化数字化制造装备及工艺过程控制;②以车间作业调度、物流管理等为基础的数字化车间生产过程管理,如MES系统;③产品数字化开发、设计及工艺制造,包括CAD/CAPP/CAM等;④企业级资源管理、对外商务及营销数字化管理,包括企业资源计划(ERP)、产品数据管理(PDM)、电子商务、供应链等管理等。
生产现场数据的获得和集成是生产组织、决策的重要依据,是企业信息化工作中必不可少的重要组成。上级信息管理系统只有采用来自工艺系统当前运行的实时数据,而不是沿用历史数据,其调整优化结果才能达到最优。
现代化制造装备正向着复杂化、大型化、高速化、自动化、智能化方向发展,实现对其运行状态远程监控及(设备及工艺)运行诊断,能够有效组织生产,提高设备的利用率,提高产品质量,降低生产成本,最终提高企业的核心竞争力,使企业在激烈的市场竞争环境中取得更大的优势。
制造执行系统MES(Manufacturing Execution System)、SIS、数字化企业等做法,在很大程度上填补了管理系统与底层控制层之间的鸿沟。MES最初是20世纪90年代美国管理界提出的,MES国际联合会对MES的定义如下:MES能通过信息传递对从订单下达到产品完成的整个生产过程进行优化管理。当工厂发生实时事件时,MES能对此及时做出反应、报告,并用当前的准确数据对它们进行指导和处理,这种对状态变化的迅速响应使MES能够减少企业内部没有附加值的活动,有效地指导工厂的生产运作过程。
但从实施来看,由于企业生产的差异,不同行业、不同企业的MES有很大的差别,企业性质及建模目标的不同,企业模型可以分为多种不同层次水平和视角的模型形式,造成MES规范性差;金字塔递阶控制结构层次较多,对数据的共享与各功能软件的维护的困难大。
所以,目前的实时数据集成系统多摒弃以往的多层次结构而采用“扁平结构”,如图1-17所示,提出信息化环境下控制系统对管理系统的统一数据服务的概念,以简化开放的形式将信息化“一网到底”。扁平结构信息流形式清晰,减少纵向数据传输的层次,简化管理的复杂程度,在结构上具备良好的可靠性、开放性,同时增加横向系统间的联系,使其适应现代化制造的发展。

图1-17 制造系统控制网络及其集成
现场总线/工业以太网技术随着PLC的广泛应用已经作为现场数据采集网络的首选,控制器、采集装置接入到现场总线控制网络中产生新的结构形式,如图1-18概况了当前的基于网络的先进控制系统的结构。特别指出,随着基于数字通信的CNC系统及基于iPC的开放式CNC的发展,CNC系统在基于现场总线的控制网络中结构有所改变,控制器从整个控制核心变成现场总线网络上的节点,与其他部分的通信完全依靠总线网络,作为一类主站其节点的地位与其他设备可能完全相同,在逻辑功能上还处于核心的地位。

图1-18 控制系统基于控制网络的集成