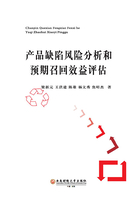
1.2 缺陷汽车产品的召回流程与效益评估
国家缺陷产品管理中心的陈玉忠和清华大学汽车安全与节能国家重点实验室的刘晨提出了缺陷调查与召回监管主要流程,量化分析了2004—2014年的汽车产品召回进行汽车产品召回管理的经济效益,指出在汽车产品的召回率、召回完成率以及召回效能比等方面,中国与美国相比仍有很大差距。
缺陷调查与召回监管主要流程如图1-1所示,确定了缺陷调查所处的阶段。

图1-1 缺陷调查与召回监管流程图
召回率Rr(Recall Rate)被定义为年度召回汽车数量Nr与年度销售汽车数量Ns之比,即:

美国汽车召回率平均在1以上,即市场上每销售一台汽车,就有一辆已经销售出去的汽车会因为某个缺陷而被召回,这从一个侧面反映出美国召回制度和管理工作已经非常成熟。相比较而言,中国汽车市场高速发展,但市场监管能力仍然较弱,两者的发展速度不匹配,导致中国汽车产品召回率目前仅为0.2。
本节引用的召回率与汽车工业中所用的“召回完成率”不同。“召回完成率”是指召回的完成情况,是一项反映召回效果的指标。影响召回率的因素较多,欧洲的一项研究结果表明:车型数量、制造商的地域属性、制造商的召回策略等都会对召回率产生一定的影响。
陈玉忠进行了召回的经济效益分析。在召回发起后,生产者需要通过修、退、换的方式来消除缺陷。在召回实施过程中,生产者需要确定消除方案、生产部件、分配物流、货物管理、联系车主、检测维修等多方面的工作,形成直接召回成本。此外,Mc Donald等人的研究表明:召回对生产者的股票、市场份额、品牌形象和未来收益的影响远远大于召回的直接成本。由于缺乏相关间接召回成本数据,陈玉忠对国内生产者的直接召回成本进行统计分析。根据中国主要汽车系统召回成本统计,2013—2014年的120例召回费用的详细统计结果表明:每次召回平均费用在7041万元,单车单次召回费用为1970元。排除由于实施措施或处置方式不当而导致召回费用远高于其他召回的个别召回事件,分析表明,每笔召回平均费用为1474万元,单车每次召回费用为497元。
汽车召回工作为消费者挽回的直接成本P与国家直接投入召回工作经费C的比值为召回效能比Rs:

2004—2014年,中国汽车召回工作为消费者挽回的直接成本P=284亿元,政府对缺陷汽车产品召回工作的经费总投入C=9300万元。因此,中国汽车召回工作召回效能比为305。国家在汽车召回工作中每投入1元人民币,相当于为消费者直接挽回305元的经济损失,切切实实地消除了车辆缺陷对于人身财产安全的威胁。当然,我们还可以从不同的角度来进一步分析这一组数据,譬如从召回业务工作本身来看,上述召回效能比反映了中国对缺陷汽车产品召回工作以较小的投入取得了较好的成果。