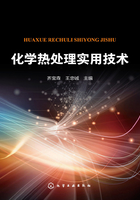
第2章 渗碳工艺及其应用
2.1 概述
所谓渗碳是将工件放入渗碳气氛中,并在900~950℃的温度下加热、保温,使其表面层增碳的一种工艺操作。它是金属材料最常见、应用最为广泛的一种化学热处理工艺。即渗碳是向金属表面层渗入碳原子的过程,其目的是使工件在继续经过相应热处理后表面具有高硬度和耐磨性,而心部仍保持一定强度和较高韧性。渗碳工艺广泛用于飞机、汽车和拖拉机等的机械零件,如齿轮、轴、凸轮轴等。
2.1.1 渗碳工艺特点及对渗碳层的技术要求
2.1.1.1 渗碳工艺的特点
渗碳是一种历史悠久、应用广泛的化学热处理工艺,它具有表2.1所列的特点。
表2.1 渗碳化学热处理工艺的特点

2.1.1.2 渗碳工艺的适用场合
对于在交变载荷、冲击载荷、较大接触应力和严重磨损条件下工作的机器零件,如齿轮、活塞销和凸轮轴等,要求工件表面具有很高的耐磨性、疲劳强度和抗弯强度,而心部具有足够的强度和韧性,采用渗碳工艺可满足其性能要求。
2.1.1.3 对渗碳层的技术要求
对渗碳层的技术要求见表2.2。
表2.2 对渗碳层的技术要求


图2.1 表面碳浓度对钢的力学性能的影响
表2.3 表面碳浓度对20CrMnTi钢弯曲疲劳强度的影响

注:1kgf=9.81N。

图2.2 渗层深度和心部强度对零件承载能力的影响

图2.3 渗碳层深度对钢力学性能的影响
表2.4 各种齿轮渗碳层深度的推荐值

①m为齿轮模数。
表2.5 机床渗碳零件的渗碳层深度

2.1.2 渗碳层的测定
渗碳层的测定方法见表2.6。
表2.6 渗碳层的测定方法

表2.7 渗碳淬火试样进行渗层深度检查前的热处理规范

表2.8 20CrNi2MoA钢不同试样截面所得渗碳层深度与有效硬化层深度间关系

2.1.3 渗碳用钢及渗碳前的预备热处理
2.1.3.1 渗碳用钢
渗碳用钢的化学成分特点见表2.9。典型渗碳钢的特点及应用见表2.10。表2.11为不同条件下使用的各种低速重载及高速齿轮用渗碳钢。常用渗碳钢的牌号、化学成分、热处理、力学性能及用途见表2.12。
表2.9 渗碳用钢的化学成分特点

表2.10 典型渗碳钢的特点及应用

表2.11 不同条件下使用的各种低速重载及高速齿轮用渗碳钢


2.1.3.2 渗碳钢中合金元素的主要作用
合金元素在渗碳钢中的主要作用,见表2.13。
表2.13 合金元素在渗碳钢中的主要作用


图2.4 沿钢的渗碳层深度的碳浓度分布
1—碳钢;2—以碳化物元素合金化的钢;3—以非碳化物元素合金化的钢

图2.5 925℃渗碳时合金元素对渗碳层深度影响
2.1.3.3 渗碳钢渗碳前的预备热处理
为改善钢的切削加工性,使其心部组织均匀,减少渗碳淬火后的变形,渗碳前钢坯应实施正火或正火+回火处理,以获得粒状或细片状珠光体(P)+少量铁素体(F)或索氏体(S)组织。常用渗碳钢的预备热处理工艺、显微组织和硬度见表2.14。
表2.14 常用渗碳钢的预备热处理工艺、显微组织和硬度

2.1.3.4 渗碳件的表面清理与防渗处理
工件渗碳之前应进行脱脂、除锈及除垢处理。通常采用质量分数为1.5%~3.0%的碳酸钠水溶液,也可用专用脱脂剂。若铁锈较重,可采用喷砂处理。清洗后应将工件充分干燥,不允许将水分带入渗碳炉。
工件非渗碳表面可采用增大加工余量法、镀铜法、涂料防渗法、紧密固定钢套及轴环保护,不允许渗碳部位等进行防渗处理。各种防渗处理方法的技术要求见表2.15~表2.17。
表2.15 非渗碳面预留加工余量(于渗碳后切除)

表2.16 防渗碳镀铜层厚度

表2.17 常用防渗碳涂料的组成及使用方法

2.1.4 渗碳介质与碳势控制
2.1.4.1 渗碳介质
常用渗碳剂的主要组成、特点及使用方法见表2.18。在渗碳过程中,按介质作用的不同又可分为渗碳剂和稀释剂两种。几种常见渗碳剂分解后的产气量与产生炭黑的量见表2.19。
表2.18 常用渗碳剂的主要组成、特点及使用方法

表2.19 常见渗碳剂分解后的产气量与产生炭黑的量

2.1.4.2 常用渗碳剂简介
常用的几种渗碳剂及其特点见表2.20。
表2.20 常用渗碳剂及其特点


图2.6 煤油在不同温度热分解时烃类含量的变化
表2.21 气体渗碳时煤油分解气成分(%)

表2.22 苯的热分解气成分(%)

2.1.4.3 渗碳过程的化学平衡及炉气碳势控制
气体渗碳主要是依靠渗碳气氛中的CO及CH4在高温下分解出活性碳原子而实现的,温度、时间、渗碳剂的供给量对钢的渗碳质量有明显的影响,其渗碳过程分为供碳和吸碳两个方面。
液体渗碳剂滴入炉内,在高温下发生分解,其产物为CH4、不饱和烃类、CO、CO2、H2、O2及N2等。据报道,CH4的渗碳能力很强,CO较弱。在高温下氢的脱碳能力并不强,相反可延缓烃类的分解过程,阻止不饱和烃类的形成和炭的产生,从而保护钢的表面不被氧化。
由此可见氢通常作为稀释性保护气体,不渗入,只起稀释和保护作用,氧气与二氧化碳对工件有氧化作用,渗碳气氛中CO及CH4在高温下分解,其反应式为:
因此炉内混合气体的渗碳能力是气体各组成渗碳和脱碳的综合表现,随成分的变化,反应可以朝着不同的方向进行,当反应达到动态平衡时工件既不脱碳也不增碳,工件与炉气之间碳的交换处于相对平衡状态,这时工件表面的碳含量称为碳势。当炉气中的碳势高于工件表面的碳含量时发生渗碳反应,反之则发生脱碳反应。根据化学平衡原理,此时反应物与生成物的分压不变,其比值为一个常数,炉内混合气体发生增碳或脱碳反应取决于炉气中CO/(CO+CO2)和CH4/(CH4+H2)的比值,同时与钢种的碳含量有关。
碳势只取决于CO2和CH4的含量,炉内碳势主要因素为CO2,即碳含量与CO2含量呈反比关系,这可借助于CO-CO2-Fe和CH4-H2-Fe平衡图予以说明。
CO-CO2-Fe的平衡图见图2.7。从图中可知:①在abc线左面,CO2含量较高,Fe被氧化成FeO,不存在渗碳反应,abc线为氧化和还原分界线;②abed围成的区域为铁素体稳定区;③def右面是渗碳体的稳定区,由于CO含量较高,可在钢中直接形成渗碳体;④cbef线围成的区域为碳含量可变的奥氏体稳定区,此区域中各条曲线为碳含量不同的奥氏体渗碳和脱碳的平衡曲线。当温度一定时,CO的相对含量越高,奥氏体平均碳含量越高,即CO相对含量高的炉气具有高碳势,而当CO相对含量一定时,温度越高奥氏体的平均碳含量越低,易脱碳,表明有CO-CO2组成的炉气中,其渗碳能力随温度的升高而下降。

图2.7 CO-CO2-Fe的平衡图
CH4-H2-Fe平衡图见图2.8。图中SE与SP围成的区域为碳含量可变的奥氏体区,SP左面区域为铁素体的稳定区,SE右边区域为石墨与奥氏体共有区,该图分为三个区域,其分析方法同上。当CH4相对含量一定时,温度越高奥氏体的平均碳含量越高,即CH4-H2组成的炉气中其渗碳能力随温度的升高而增大。

图2.8 CH4-H2-Fe平衡图
CH4的活性远远大于CO。在900℃要使钢表面碳含量达0.8%,需95%以上CO,如用CH4则需要量不到1.5%。在实际生产中,多种气体混合在一起的作用十分复杂,其表面碳含量为各种气体渗碳和脱碳共同作用的结果。炉内的化学反应都没有达到平衡,只是趋于平衡,了解这些化学反应的平衡条件,为选择渗碳介质和控制工艺提供了理论基础。
2.1.5 渗碳后的热处理与渗碳层的组织、性能
2.1.5.1 渗碳后的热处理
对渗碳钢来说,要求表层硬度高、强度高、耐磨性好,而心部应有良好的韧性。只有通过渗碳得到表面和心部成分的差异,然后经恰当的热处理,才能强化表层,提高耐磨性,并获得具有良好韧性和一定强度的心部组织。渗碳后热处理的目的见表2.23。渗碳件热处理方法的选择及要求见表2.24。
表2.23 渗碳后热处理的目的

表2.24 渗碳件热处理方法的选择和要求

表2.25列出了零件渗碳后的冷却形式。根据工件的成分、形状和力学性能的要求,选择不同的热处理方式。渗碳后常用的几种热处理方法,可根据零件材料和性能要求来作恰当的选择,见表2.26。
表2.25 渗碳后常用的冷却方式与适用范围

表2.26 渗碳后常用热处理工艺的名称、特点及适用范围



图2.9 渗碳后直接淬火+低温回火

图2.10 渗碳后常用的热处理方法

图2.11 渗碳,高温回火,一次加热淬火,低温回火,淬火温度840~850℃

图2.12 二次淬火+冷处理+低温回火

图2.13 渗碳后感应加热淬火+低温回火
渗碳件的淬火处理,可在井式炉、箱式炉和盐浴炉中进行,为防止加热时氧化脱碳,在井式炉、箱式炉中应滴入煤油或通入保护气氛。盐浴炉脱氧充分,根据材料的成分、性能要求等不同,选用合理的淬火介质(油或盐水等)。对于形状复杂、有尖角和沟槽、厚度悬殊较大的工件,为防止开裂和变形,可采用分级淬火。采用上述方法,使渗碳后工件达到表面硬度高、心部韧性好的目的,在使用过程中发挥了良好作用,因此应用较广泛。
2.1.5.2 渗碳层的组织与性能
渗碳层的组织与性能见表2.27。表层及心部组织对渗碳件性能的影响见表2.28。
表2.27 渗碳层的组织与性能



图2.14 缓冷后渗碳层的金相组织(100×)

图2.15 10钢经渗碳、淬火、回火后表层、过渡区及心部的组织形貌(500×)
表2.28 表层及心部组织对渗碳件性能的影响

总之,渗碳件经热处理(淬火+低温回火)后,获得合适的组织结构,方能达到较高的力学性能要求。一般认为工件渗碳层表层组织为M回+K粒+Ar(少量),硬度56~64HRC;心部淬透时组织为低碳M回+F(少量),硬度30~45HRC(心部未淬透时,组织为F+P,硬度相当于10~15HRC)。渗碳层不允许出现网状碳化物,淬火后渗层中的Ar应在允许范围之内,应避免氧化脱碳和淬火变形;心部组织不允许有大块F存在。此时工件畸变最小。