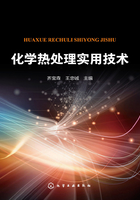
第3章 碳氮共渗工艺及其应用
3.1 概述
碳氮共渗(俗称氰化)系指在奥氏体状态下同时将碳、氮渗入工件表层,并以渗碳为主的化学热处理工艺。其目的是使工件在保持心部较高韧性的条件下,表面层获得高硬度,以提高其耐磨性和抗疲劳性能等。
碳氮共渗层比渗碳层具有更高的耐磨性、疲劳强度和耐蚀性;比渗氮层有更高的抗压强度和更低的表面脆性,而且生产周期短、渗速快、适用材料广泛。碳氮共渗的性能和工艺方法等与渗碳基本相似,但由于氮原子的渗入,又有其特点。
3.1.1 氮原子的渗入对渗层组织转变的影响
氮原子的渗入对碳氮共渗渗层组织转变的影响,见表3.1。
表3.1 氮原子的渗入对碳氮共渗渗层组织转变的影响


图3.1 20钢[成分(质量分数):C 0.17%~0.24%,Si 0.10%~0.20%,Mn 0.30%~0.60%]碳氮共渗和渗碳层端淬曲线对比
3.1.2 碳氮共渗的特点
(1)碳氮共渗化学热处理的特点 见表3.2。
表3.2 碳氮共渗化学热处理的特点

表3.3 氮和碳对临界点的影响


图3.2 碳、氮在共渗层中的分布曲线

图3.3 温度对碳氮共渗层和渗碳层深度影响
(2)碳氮共渗的工艺特点 见表3.4。
表3.4 碳氮共渗的工艺特点


图3.4 共渗温度对共渗层中碳、氮含量的影响
(a)50%CO+50%NH3气体;(b)23%~27%NaCN盐浴;(c)50% NaCN盐浴共渗;(d)30% NaCN+8.5% NaCNO+25% NaCl+36.5%Na2CO3

图3.5 碳氮共渗时间对渗层碳、氮含量的影响
(a)不同保温时间下共渗层表面碳、氮含量(T8钢,温度800℃,渗剂:苯+氨);(b)不同保温时间下共渗层截面中氮含量分布(30CrMnTi,渗剂:三乙醇胺,温度850℃)
3.1.3 碳氮共渗工艺的分类
碳氮共渗工艺的分类见表3.5。
表3.5 碳氮共渗工艺的分类

3.1.4 碳氮共渗的技术条件
碳氮共渗的技术条件见表3.6。
表3.6 碳氮共渗的技术条件

表3.7 齿轮类工件的碳氮共渗层深度要求

表3.8 按照服役条件、承载能力选取共渗层深度的要求

3.1.5 碳氮共渗用材及共渗后的热处理
(1)碳氮共渗用材 见表3.9。对碳氮共渗用钢力学性能、工艺性能及钢材质量方面的要求与渗碳钢基本相同,因此一般渗碳钢均可用于碳氮共渗。
表3.9 碳氮共渗工艺适用的材料范围

(2)碳氮共渗后的热处理 与渗碳相比,碳氮共渗过程处理温度较低,一般不会发生晶粒长大,故共渗后通常进行直接淬火和回火。常用结构钢碳氮共渗后热处理工艺及表面硬度见表3.10。碳氮共渗零件热处理各工艺方案的特点见表3.11。
表3.10 常用结构钢碳氮共渗后热处理工艺及表面硬度

表3.11 碳氮共渗零件热处理各工艺方案的特点


3.1.6 碳氮共渗件的组织与性能
碳氮共渗件的组织与性能见表3.12。
表3.12 碳氮共渗件的组织特征与力学性能


图3.6 低碳钢碳氮共渗后的平衡组织(100×)

图3.7 40Cr钢齿轮共渗后直接淬火组织(100×)

图3.8 850℃碳氮共渗和渗碳淬火硬度比较(20Mn2TiB钢)
表3.13 几种钢碳氮共渗及渗碳后的耐磨性对比
