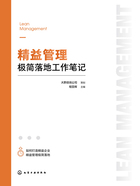
1.4 制造层面——有效产出的效率稳定
1.4.1 通过制造方法的改变,实现削减成本的目的
精益希望达到的理想生产状态就是,彻底地消除浪费,实现成本削减。这里所讲的浪费,指的是成本结构树中存在的损失,而非精益中的七大浪费现象。
1.4.1.1 精益中提到的七大浪费
精益中提到的七大浪费,指的是生产现场存在的七种浪费现象,分别是过量生产的浪费、等待的浪费、搬运的浪费、加工本身的浪费、动作的浪费、生产不良品的浪费、库存的浪费。提出七种浪费现象的目的,是希望全员具备浪费消除意识,能够在日常工作中识别浪费,继而提出针对浪费的改善建议。识别七种浪费现象的活动,通常要与创意功夫提案活动一并使用,以鼓励全员参与改善。严格意义上来讲,识别七大浪费的活动,是带动基层员工提出合理化建议时使用的方法。
1.4.1.2 成本损失的浪费
成本损失的浪费,指的是成本结构树中材料费、人工费、制造费等方面存在的成本损失。往往是由于对新产品设计、原辅材料利用率、生产工艺和加工方法的设置、生产布局的设计、人员技能的偏差、设备加工效率、能源利用效率等考虑不周,所带来的成本损失。产品成本的组成项目,如表1-1所示。
表1-1 成本的组成项目

减少损失,首先要对工厂存在的损失进行调查,损失项目的分类见图1-6。由于工厂的产品类别和加工工艺不同,需要根据工厂的实际情况,对损失现象进行定义,见表1-2。

图1-6 损失项目的分类
表1-2 损失现象的定义

续表

对工厂存在的损失进行详细的定义,目的是要在管理与成本之间建立关联。通常,负责成本计算的财务人员,由于不了解实际的生产工作,无法提出成本改善的具体建议。而了解日常工作的管理人员,由于无法掌握管理损失导致的实际成本金额,不能开展有针对性的经营成本改善活动,造成管理重点和成本关注重点不能聚焦,错失改善机会,甚至还会使财务管理和生产管理之间产生误解。如果在损失现象和成本之间建立关联,见表1-3,就等于在管理行为和成本管控之间建立了沟通的桥梁,能够对损失进行更直观、更系统的识别和改善。
表1-3 损失现象和成本科目关联

1.4.1.3 成本损失和七大浪费之间的关联
经营层面提出的浪费,指的是上述所谈的成本损失。削减成本损失的改善活动和识别生产过程中七大浪费的活动,有着很大的不同。成本损失和七大浪费之间的关联如表1-4所示。
表1-4 成本损失和七大浪费之间的关联

1.4.2 始终关注并提升有效产出,通过持续改善,打造稳定的生产体制
制造层面的精益活动,始终以稳定有效的产出为目的。
1.4.2.1 有效产出的含义
所谓的有效产出,是指制造出来能够直接交货、直接回款的良品。精益企业的理想经营模式是按需生产,客户需要时才启动生产,成品生产出来后,以不早不晚“刚刚好”的时间交付给客户。所有按客户需求直接交付的产品,就是有效产出。即便是客户的正式订单,产品未到交货日期就提前生产出来,也不是有效产出,反而被定义为提前生产的浪费和库存的浪费。
在客户需要时刚好把成品制造出来,需要非常稳定的生产过程。如果生产过程经常因异常因素发生生产中断或停顿,那么就会带来不能及时交货的风险。很多企业,正是因为生产过程中发生异常的概率很高,所以才不敢在临近交货时启动生产,越是尽早生产,才越会安心。启动生产的时机,是精益企业和传统企业之间的显著差异之一。
稳定的生产,一方面意味着能够及时完成生产计划,所以通常使用计划达成率来衡量生产的稳定性;另一方面又意味着生产过程中不会出现导致生产中断和停顿的异常因素。如果企业生产过程中发生异常的概率很高,却又表现出很高的计划达成率,说明生产任务远低于生产能力;或者为了让计划达成率的数据变好,安排生产计划时预留了过多的余量,这说明制订生产计划的工作,存在浪费(余量)。
打造稳定的生产过程,需要事前预防异常的发生,并建立异常发生后的快速处理机制。出现的异常现象和导致的结果,会记录在生产报表中,企业通常会建立异常报告、处理和统计的管理机制。对生产过程曾经发生的异常现象进行分析,并制定事前识别和预防的措施,可有效防止异常的出现。只要企业对曾出现的异常有充分的记录和预案,后续生产过程中就可以事前识别和预防该异常现象。某种意义上,能否事前预知异常的发生并采取有效的预防手段,是衡量管理人员管理能力的一项重要内容。管理的意义不只是把确定的工作做好,还在于把不确定的工作变为确定。做好事前管理、预防异常发生,是管理人员应当重点关注的工作。但多数情况下,善于事后采取补救措施的管理人员,往往更容易获得重视和好评。之所以这样,是因为企业不重视事前管理。这也是企业需要注意和有必要作出调整的内容。
1.4.2.2 有效产出的衡量指标
有效产出可以从两个方面来衡量:生产计划达成率和总合效率。
(1)每日的生产计划达成率。评价每日生产计划达成率的目的在于提升每天、每班计划达成的精度。以月计划、周计划为频度来评价生产计划达成率的方式,由于间隔太长,精度反而不高。
(2)总合效率OEE。总合效率OEE(overall equipment effectiveness),是指设备或生产线实际生产能力和理论最大生产能力的比率,是衡量设备或生产线效率发挥水平的指标。计算方式如下:
设备总合效率=时间运转率×性能稼动率×良品率
其中,

负荷时间是指可以用来生产的时间,通常是出勤时间减去计划停产时间后用来生产的时间。
停机时间是指生产运转过程中存在的非计划停机现象的时间累计,比如故障、品质异常、欠料、换型等导致的停机时间。
基准周期时间(cycle time)指设备或生产线设计的节拍(tact time),通常是性能理想发挥时,以最快的生产速度加工产品的周期时间。有时以历史最高水平作为基准。
实际生产速度是现状下的实际生产速度。
运转时间指的是真正用来生产的时间,等于负荷时间减去停机时间
生产数量指运转时间内生产出来的所有产品,是包含良品和不良品在内的总生产数量。
简化后的总合效率计算公式是:

设备总合效率代表着负荷时间内,实际产量与理论最大产量的比值。该比值越大越好,比值越大,代表生产效率越高;生产效率越高,意味着单位产品摊销的生产成本越低。
既然总合效率是实际产量与理论最大产量的比值这样简单的比例关系,那为何要用时间运转率、性能稼动率、良品率的乘积来计算呢?目的是更好地改善和分工。
①时间运转率:通常由生产部门主导改善。
通常,每班或每天的负荷时间基本不变,导致时间运转率发生变化的因素,在于停机时间的多少。导致生产过程中停机的因素,通常是故障、等待物料、等待生产指示、转换型号、转换模具或刀具、转换材料、调整程序、初始开机时的设备预热(暖机)、生产过程出现的品质异常等。这些异常的预防和改善,通常由生产部门的负责人来主导。每个班发生的这些异常,也应该由生产部门记录在每班的生产日报中,并以周和月为单位进行统计和汇总,然后根据停机时间导致的损失大小,设定专门的课题进行改善,来提升时间运转率。
②性能稼动率:通常由设备部门来主导改善。
设备或生产线的性能稼动率,指的是实际生产速度和理论最大速度的差距。两者之间的差距称为速度降低的损失,通常是因为设备的性能无法充分发挥所导致的。比如,以最快的速度运转时,不良品会增加;或者设备的稳定性变差,会频繁出现短暂停机等现象。
设备的实际运转效率,通常以生产数量表现出来。在设备运转过程中,除了长时间停止(超5分钟以上)外,还会出现短暂停止(时间在5分钟内)的现象。这类短暂停止通常由操作工直接排除,并有发生频次多、恢复时间短等特征。因为记录这类现象会占用太多的时间,所以通常不把它算在影响实际运转率的停机时间内。值得注意的是,如果短暂停机的信息由设备自动采集,则可以直接归到停机时间中。这类短暂停机会影响实际运转效率,应及时作出改善。
③良品率:通常由质量管理部门主导改善。
加工过程中出现的不良品,不但会带来生产数量减少的损失,还会带来材料费、人工费的成本损失。持续不断地针对不良现象进行改善,挑战生产加工过程中的0不良,是质量管理部门的一个重要使命。
1.4.2.3 打造稳定生产体制的四个方面
打造稳定的生产体制,提升OEE,需要事前预防影响OEE的损失现象发生。影响OEE的损失现象见图1-7。

图1-7 影响OEE的损失现象
总体来讲,确保生产效率的稳定,需要做到:
(1)物料供应稳定。
(2)设备效率稳定。
(3)人员效率稳定。
(4)产品质量稳定。
如果不能确保物料供应、设备效率、人员效率、产品质量等方面的稳定,那么有效产出不可能实现真正稳定。没有稳定的有效产出,满足交货的风险会增加,就无法实现降低投入成本的均衡生产。
综上所述,打造精益企业,需要从经营环节自上而下地进行系统规划和设计,如图1-8所示。

图1-8 打造精益企业的综合管理体制