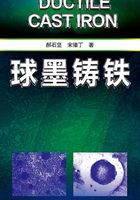
4.1 感应炉熔炼
图4-1是感应炉炉体基本结构简图。这种熔炉使用耐火材料捣制的坩埚盛装炉料和铁水。坩埚外围装有由异形铜管或矩形铜管制成的螺旋形线圈。当交流电通过感应线圈,由于交变磁场的作用,装入坩埚的炉料内产生很大的感应电流,使炉料加热、熔化并使铁水过热。按照输入炉子的电流频率,感应熔炉分为工频炉(50Hz)、中频炉(150~8000Hz)和高频炉(大于10000Hz)。按坩埚的耐火材料性质,炉子分为酸性炉、碱性炉和中性炉。按炉子结构,有无芯感应炉和有芯感应炉。

图4-1 坩埚式中频感应炉炉体结构简图
我国自20世纪70年代以来广泛使用感应炉熔炼铸铁。大型铸造厂(如汽车铸件铸造厂)多使用以大型感应炉为主体的双联熔炼。
感应炉炉料包括生铁、废钢、铸件回炉料、铁合金、切屑和增碳剂等。铁水中非金属夹杂物含量少。元素烧损率较低,铁水温度和成分易于调整和控制而达到均匀稳定。有些铸造厂还采用废钢和增碳剂熔炼合成铸铁。
由于铁水温度、成分容易控制,合金元素损耗少,感应炉可以用来熔炼高合金铁水,如高铬铸铁、高镍奥氏体球墨铸铁原铁水等。铁水比较纯净,过热温度能达到1700℃以上,元素的熔损少于冲天炉,对环境污染较轻,劳动条件相对较好,而且可使用大量废钢作为炉料,因此感应炉适用于熔炼各种球墨铸铁原铁水。但是感应炉生产的原铁水与冲天炉铁水相比,石墨晶核和石墨球数较少,铁水的共晶过冷度较大,产生白口倾向较强。温度和碳当量相同时,铁水流动性比冲天炉铁水稍差。
4.1.1 感应炉坩埚
炉料在耐火材料捣制的坩埚内熔化。熔化一般球墨铸铁的坩埚加热温度在1550℃以下。熔炼熔点更高的铁水时,坩埚还要承受更高温度。如高镍奥氏体球铁的原铁水,熔炼温度需达到1700℃。坩埚材料应能在高温下保持足够的化学稳定性、良好的高温强度和抗热冲击能力。酸性炉衬采用高纯石英砂或电熔石英砂。电熔石英砂熔点1700℃、铁水熔炼温度最高可达1600℃,适用于熔化一般球墨铸铁炉料。熔化温度更高时,还可采用锆英砂或铝镁尖晶石。锆英砂的主要成分是ZrO2,其中含有少量SiO2。ω(ZrO2+SiO2)≥95%的锆英砂熔点2500℃,最高工作温度1650℃。镁铝尖晶石是中性耐火材料。采用烧结或电熔方法把含有Al2O3和MgO矿物原料熔合在一起,制成合成耐火材料。其理论矿物组成为ω(Al2O3)=71.8%、ω(MgO)=28.2%。熔点为2135℃,用以制成的坩埚耐火度能达到1900℃。
熔炼偏碱性球墨铸铁(如无磁性奥氏体锰镍球墨铸铁)需采用碱性或中性耐火材料制造的坩埚。常用的耐火材料是烧结镁砂、电熔镁砂和镁铝尖晶石。
菱镁矿(MgCO3)经过1300~1400℃高温烧结能得到的一种以MgO为主要成分的块状物,经过破碎、筛选后制成烧结镁砂。一般烧结镁砂含MgO95%~97%。MgO熔点2800℃,优质烧结镁砂在电弧炉内再经高温熔化而制成含MgO更高、杂质含量更少,热稳定性和抗热冲击性能更佳的电熔镁砂。
坩埚采用粒状耐火材料经过捣筑、烧结后制成。粒状耐火材料的粒度需有合适配比。使各种粒度的颗粒互相嵌合,使坩埚具有良好的紧实度和高温强度。
表4-1列出两组坩埚耐火材料的粒度配比实例。经过多年实际应用,效果很好,可供参考。
表4-1 捣筑坩埚的耐火材料的粒度配比

注:筛号按ASTME11-170(77)。
坩埚耐火材料中需加入有助于烧结的添加剂。添加剂多采用硼酸(H3BO3),加入添加剂可降低烧结温度、使坩埚容易烧结成形。
捣筑前需先在感应器内侧和炉底铺设隔热层和绝缘层。并放置定位坩埚胎具。然后把混拌均匀的耐火材料分批加入,由炉底开始分层捣筑。需要注意控制好影响输入功率的炉底、炉壁厚度和均匀度。炉底或炉壁过厚会限制输入炉内的电功率,使铁水升温缓慢或达不到应有的过热温度。过薄则缩短坩埚寿命。
大型感应炉多使用电动或气动筑炉机捣筑坩埚。机械筑炉效率远高于手工筑炉,劳动条件好,而且坩埚质量比较可靠,使用寿命较长。
捣筑结束后进行炉衬烧结。烧结使颗粒状耐火材料形成能够承受炉料撞击、抵抗铁水和炉渣侵蚀的整体强固耐火坩埚。
烧结开始阶段,应以低功率向空炉送电,使钢制的坩埚成形模具升温并加热耐火材料。坩埚温度保持在900℃以下,砂料及硼酸中的水分逐渐蒸发。石英砂在870℃发生α石英向α鳞石英的同素异构转变,石英砂粒会出现很大的体积变化,因此在此区间缓慢升温十分必要。900℃升温到1200℃是烧结的主要阶段,在此阶段可向炉内加入一些炉料,利用炉料吸收的热量使坩埚升温。直到1300℃时,坩埚已经形成表面烧结层,此阶段可适当提高升温速度。在1300~1500℃区间烧结层随烧结时间加长而增厚。
新坩埚烧结后应连续进行首次熔炼。首次熔炼需将铁水缓慢加热到1500℃,保温数小时后即可结束烧结。此时烧结硬化层应达到炉壁厚度25%以上。半烧结层应超过50%。
表4-2列出熔炼普通球墨铸铁的石英砂坩埚加热烧结时间,可供参考。
表4-2 熔炼普通球墨铸铁的石英砂坩埚加热烧结时间

当前有些铸造厂使用专业工厂预制好的坩埚。更换坩埚时,先把预制坩埚放置在已捣筑的炉底层上,再捣筑周围保护层。采用预制坩埚显著缩短更换时间,而且预制坩埚质量较好,使用寿命长。比较适用于大型感应炉。
4.1.2 炉料
(1)生铁 表4-3列出我国球墨铸铁专用生铁化学成分(GB/T1412—2005)。目前国内铸造厂制造球墨铸铁多使用这种生铁,也有少数工厂使用L04、L08、L10炼钢生铁。所列球墨铸铁专用生铁所规定硅的质量分数是为了避免炉前处理使用含硅高的球化剂和孕育剂时铁水含硅量超过标准。标准规定生铁含碳量大于3.40%,便于使铁水碳当量达到共晶成分或过共晶成分。锰促进共晶碳化物和晶间碳化物生成,标准中规定锰处于较低水平。生铁的磷、硫以及强烈干扰球化的钛含量都很低。
表4-3 我国球墨铸铁专用生铁化学成分(GB/T1412—2005)

用于熔炼铁素体球墨铸铁水应采用1级含磷量,生铁中磷的质量分数对球墨铸铁的塑韧性有很大的影响。一般球墨铸铁件的含磷量不应超过0.07%。塑韧性要求较高的铸件通常规定ω(P)<0.06%。因此需使用表4-3中所列2级或1级生铁。
Q10生铁含硫量很低,1类不超过0.020%。这种生铁含锰量也很低,可用于生产铁素体球墨铸铁。珠光体球墨铸铁则宜采用含锰较高的Q12,根据铸件要求的力学性能选用2组或3组生铁。
干扰元素含量也是选择熔炼球墨铸铁所用生铁的重要因素。表4-4列出我国一些钢铁厂所产生铁的干扰元素含量。
表4-4 我国部分生铁干扰元素含量(质量分数) 单位:×10-6

(2)废钢 废钢用于降低原铁水含碳量或用于生产合成铸铁。选用废钢主要应注意它的来源、化学成分和清洁程度。钢结构件边角余料和铸钢回炉料是常用废钢。轧制件多数是低碳钢,含碳量一般不超过0.35%。但要注意有些轧制件为合金钢,例如钢轨的含锰量远超过普通结构钢,不宜用于生产铁素体球墨铸铁。废钢必须经过化验才能使用。再如使用40Cr钢铸件作为回炉料,该钢的含铬量为1.05%,加入20%就会带入铁水0.21%铬。而普通球墨铸铁允许含铬量为0.15%。使用铬钢作为部分回炉料时,铸件可能因晶间碳化物含量超过标准而报废。使用高锰钢回炉料也会发生类似问题。炉料中混入2%高锰钢就能使铁水含锰量超过标准,已不适于浇注高韧性球墨铸铁件。铸铁件回炉料也应注意化学成分问题。
(3)铁合金 铁合金种类繁多。应该实行分类保管。保管中注意勿使其受潮或沾染泥沙、油污。使用前均需根据产品出厂成分化验单配料。铁合金加入熔炉前均需在加热炉内烘烤,清除沾附的水分和油污。
4.1.3 加料与熔化
中频感应炉修炉结束后即可把炉料分批加入。工频炉冷炉起熔时,需首先加入起熔块(重量占炉子容量10%~30%)。热炉则需保留前一炉部分铁水。分批加料时应先加入熔点较低的炉料,尽快熔化出铁水,这样可以缩短熔炼时间,减少熔化电耗。
铁合金可在炉料熔化2/3~3/4时或随最后一批炉料加入。熔点高、烧损率大的铁合金应尽早加入。熔点低、烧损率小的合金可后加入。加入铁合金时尽量避免与炉渣接触,减少铁合金损失。
所有炉料均需经过清理。黏砂、潮湿、锈蚀、涂过油漆的炉料必须清理干净后再加入铁水。切屑可在炉料熔化一半后加入,一次加入量不要超过炉子容量的10%。切屑必须清洁、无油污、无锈蚀,确知其来源和成分。
熔化中应避免炉料在坩埚内交叉支撑,防止“搭桥”。搭桥是感应炉熔化作业中的危险状况。因为炉料不能下降到坩埚下部已熔铁水中。输入炉内的电功率集中在坩埚下部的少量铁水,使底部铁水过度加热,急剧侵蚀坩埚下部的炉衬,可能造成漏炉事故。发现红热状态炉料交叉支撑阻碍炉料下落时,必须及时将其分离。
炉料化清后应及时除渣,然后开始提高铁水温度,测定和调整铁水成分、进行炉前检测。扒渣应在1400~1500℃以前进行,因为超过1450℃,部分熔渣变稀,较难扒除。
铁水化学成分合格并达到预期过热温度后,应尽快扒渣出炉。铁水在铁水包中静置数分钟后即可开始浇注。
4.1.4 感应炉坩埚损伤与维修
熔炼过程中,坩埚不断遭受炉料撞击、铁水冲刷、炉渣和铁水中元素与炉衬间的化学反应以及热应力作用后、将会受到侵蚀和损伤。侵蚀和损伤可能发生在不同部位,如图4-2所示。

图4-2 坩埚损伤部位
图4-2(a)显示加料时炉料对炉口多次撞击造成的损伤。这种损伤常出现在分批加料的坩埚上。与其他类型损伤相比,这种损伤对坩埚寿命影响相对较小。图4-2(b)显示炉内铁水强烈搅动对炉壁剧烈冲刷产生的侵蚀。炉料在坩埚内搭桥(棚料),造成坩埚下部铁水过热,并在炉内较长时间停留时发生的损伤如图4-2(c)所示。这种损伤容易造成漏炉事故,操作者需要注意及时处理搭桥炉料。图4-2(d)显示铁水表面炉渣对坩埚的侵蚀。如果铁水表面扰动剧烈,这类侵蚀加重。图4-2(e)和(f)类损伤形成的原因相同,只是图4-2(e)类液面波动剧烈。图4-2(g)是由于感应器线圈与炉底的相对高度不合适或炉料搭桥造成坩埚下部铁水过热所致,也是一种比较危险的损伤。
长期使用感应熔炉的经验告诉我们,化学侵蚀、坩埚内壁结瘤、坩埚开裂是直接影响坩埚寿命的三个原因。下面以酸性炉衬(石英砂坩埚)为例说明。
酸性坩埚的化学侵蚀实质上是坩埚材料(二氧化硅颗粒)在高温下熔入炉渣的过程。构成炉渣的主要成分是铁水氧化产生的氧化物或锈蚀炉料带入的氧化铁(FeO)、三氧化二铝(Al2O3,富含于膨润土中,随回炉料中未清除干净的型砂带入)以及铁水氧化形成或炉料中含有的熔渣带入的二氧化硅组成。组成物达到一定比例时,炉渣熔点下降。例如当渣中含有40%SiO2、10%Al2O3、50%FeO时,渣的熔点只有1083℃。而新形成的渣中SiO2含量不足,在渣与炉衬表面接触时,炉衬中的SiO2最易熔入渣中,加快炉衬损耗。当渣中含有MnO、CaO等碱性化合物时,SiO2熔入渣中的速度加快,导致坩埚更快损耗。铁水含碳量较高时,能减少SiO2向炉渣转移。有助于延长坩埚寿命。
炉子使用一段时间后坩埚内表面可能出现局部凸出,该部分壁厚增加。炉膛内径随之缩小,这种现象称为结瘤。结瘤现象来源于石英砂、铁水和(或)其中Al2O3、MnO等化合物的反应。形成的复合化合物熔点高于铁水过热温度,便沉积在坩埚内壁,形成结瘤。为了避免产生结瘤,应尽量减少炉渣中Al2O3含量。Al2O3主要来自回炉料中未清除干净的膨润土或含铝的铸铁回炉料。另外需要避免低温铁水在炉中停留时间过久,因为铁水温度较低时,结瘤的生成显著加快。
冷态下难以铲除结瘤。可以采用“洗炉”方法去除结瘤[2]。方法是在炉内装入生铁,当铁水温度达到1200℃时加入适量冰晶石,冰晶石加入量以熔化后能在铁水表面形成薄层熔渣为准。铁水继续升温到1500℃时,进行保温20min至1h,保温期间应使炉体前后倾动。由于铁水在坩埚内不断上下循环流动,冰晶石形成的稀溶液不断冲刷炉壁上的结瘤,使结瘤中的氧化物,硅酸盐等物溶入渣中,结瘤将会减小,最终消失。
冰晶石对酸性炉衬有较强烈的侵蚀性,在高温下侵蚀速度很快。因此在浸洗炉衬过程中,操作者要仔细观察炉壁结瘤的变化情况。一旦发现结瘤消除,必须尽快降低输入炉内的电功率,并在液面加入除渣剂,迅速扒除熔渣。
铁水出炉后,炉衬温度会发生骤然变化。导致坩埚内产生热应力。这种热应力是造成炉壁开裂的重要原因。炉壁开裂是严重的坩埚损伤。
炉壁裂纹有两种基本形式。沿炉壁圆周的环状裂纹或沿炉壁高度的轴向裂纹。环状裂纹通常是不连续的。这种裂纹随熔炼次数增多而不断扩展。比较容易造成事故,因为铁水可能向裂纹缝隙中渗透,当裂纹穿透坩埚壁时,将会发生漏炉事故。而轴向裂纹通常发生在停炉后坩埚冷却过程中,在热应力作用下,因炉衬材料发生较大的不均匀收缩而产生。这种裂纹可能在再次加热时因耐火材料热膨胀而闭合。经过合理修补的轴向裂纹不致迅速扩展。
为了避免裂纹的产生,要注意坩埚捣实的紧实度。内部孔隙过大的坩埚容易出现开裂。烘炉和烧结过程中,一定要严格遵守加热规范,避免过快升温。达到烧结温度并保持一定时间后要及时开始熔化作业。新炉衬初次熔化应使铁水尽可能达到最高过热温度、并连续熔化多炉,使炉衬充分烧结。
日常熔化时,应避免坩埚骤冷骤热以及炉内储存铁水成分频繁变化。浇注完毕而不再连续熔化时要及时盖好炉盖,并适当加入一部分下次开炉所需炉料。
每次熔炼后,操作者都要对炉衬侵蚀程度、有无开裂和裂纹是否扩大、有无结瘤和结瘤程度进行检查。发现坩埚内部出现以下情况,要及时修补。
①炉子冷却后,坩埚上部出现深度超过炉壁厚度1/3;下部出现深度超过炉壁厚度1/4的轴向开裂。
②坩埚内部出现断续的环状裂隙,多处裂隙的总长度不超过坩埚内壁展开长度1/5。
③炉壁侵蚀深度超过新炉衬壁厚1/4;炉底及其与周边炉壁连接处的侵蚀深度超过炉底厚度1/4。
修补前需将损伤部位清理干净,不能存在炉渣、残铁。然后在酸性炉衬修补处的表面涂刷硼酸水溶液,再将混拌好的修炉材料(与新炉所用材料相同)填入被侵蚀部分(或裂隙中),并用木槌将填入的材料捣实。然后及时装入炉料,通电升温(升温不宜过快)至1500℃左右,使修补处的耐火材料烧结。如果修补面积不大的话,经过适当高温保温后,即可继续进行熔化作业。为了防止发生漏炉事故,超过上述损伤程度的炉衬,需要更换炉衬。将坩埚拆除,按前述方法,重新捣筑新炉衬。
4.1.5 熔炼中常存元素含量的变化
常存元素在熔化过程中受到氧化或与其他元素化合,形成的化合物进入熔渣或形成气态化合物逸出铁水。这是造成元素减失的主要原因之一。
(1)碳、硅质量分数的变化 在铁水熔化温度下,铁及其中的碳和硅都要受到氧化。分别生成FeO、CO、SiO2。铁水中过饱和氧与铁反应生成的FeO以及炉料带入的FeO参加SiO2和CO之间的转换。这种反应处于平衡状态时,SiO2和CO转换反应可写为:
(4-1)
根据热力学可以计算出这个反应的平衡温度,或者在一定温度下反应达到平衡时的碳、硅含量。图4-3为根据计算参数绘成的线图[1]。由右侧成分轴上的ω(C)成分点和左侧成分轴上的ω(Si)成分点连接线与中间坐标线相交,交点显示反应转换的理论温度(左侧坐标值)与实际测定的转换温度(右侧坐标值)。

图4-3 Si-C反应平衡温度及铁水必要的过热温度
实验表明:在低温阶段的硅氧反应到达某一临界温度后即停止下来,超过此温度后继续加热,则溶解氧与碳开始碳氧反应CO)此临界温度与铁水中碳和硅的含量有关。根据热力学计算,此值在1350~1450℃之间。例如,ω(C)=3.0%,ω(Si)=2.0%时,此反应的平衡温度为1425℃,此温度是氧存在状态的温度界限。低于此温度硅以SiO2状态存在,碳仍存在于铁水中。高于此温度SiO2被还原,碳被氧化生成CO逸出铁水。这表明超过平衡温度时,铁水中碳质量分数减少,硅质量分数增加。
经过实际测定,此反应转换温度总是超过计算温度约50℃。这是因为氧由SiO2中转入CO要经过还原过程,而CO气泡需要经过形核和生长过程,此过程在高于平衡温度下才能完成。因此对于球墨铸铁原铁水来说,此温度界限通常定为1450℃。
了解和掌握两种反应的转换规律和转换温度,对于球墨铸铁原铁水的熔炼是重要的。因为这种转换对于原铁水的含氧量有影响,而且也可据此预测铁水的碳、硅含量变化,合理判断铁水的预期成分,正确掌握铁水过热温度和浇注温度,在合适的温度进行除渣作业。这些对于球墨铸铁的炉前处理以及铸件的最终质量都有重要影响。
图4-4显示酸性感应炉铁水在1350~1630℃保温过程中碳和硅质量分数变化的实测数据。1350℃保温时、碳和硅含量几乎都没有发生变化。1450℃时碳含量下降、硅量略有上升,表明硅开始还原,碳被氧化为CO。进一步提高保温温度时,含碳量显著下降,说明此时铁水中的碳已经大量氧化而随CO逸出铁水,SiO2也大量还原(包括石英砂炉衬和外来的SiO2粒子),导致铁水含硅量急剧上升。此图可以反映上述由热力学计算得出的结果[2]。

图4-4 酸性感应炉保温过程中铁水硅、碳含量变化
表4-5显示另一组实验数据,也显示出温度对ω(Si)=1.8%~2.2%铁水中碳和硅质量分数变化的影响。
表4-5 铁水温度对ω(Si)=1.8%~2.2%铁水中碳和硅质量分数变化的影响

(2)锰质量分数的变化 氧与锰的亲和力弱于氧与硅的亲和力。锰在铁水中的损失主要来源于锰和氧、锰和硫的化合。锰与耐火材料及铁水氧化提供的酸性化合物相结合形成稳定化合物并转入炉渣,使锰遭到损失。在酸性炉衬中熔化时,炉料中锰的总损耗量为3%~8%。
加入铁水的锰铁中锰的损耗约为10%。碱性炉中锰的总损耗高于酸性炉,约为15%。
磷质量分数在铁水熔炼过程中没有明显变化。
(3)硫质量分数的变化 球墨铸铁原铁水含硫量是铁水质量的一项指标。感应炉熔炼过程中硫的变化并不显著,硫主要消耗于球化处理时与镁、铈、锰的化合,所形成的化合物进入熔渣。加镁处理后,硫将降低到0.02%以下。如果原铁水含硫过高,可能与硅酸镁结合,在铸件中形成夹渣缺陷。而且在球化处理(加镁和稀土)后,容易发生回硫现象,使球化处理效果变得不稳定。但是硫的质量分数不能过小,因为硫化物是球状石墨形核基质中的主要组成物。
4.1.6 铁水中加入的合金料
为了改善球墨铸铁性能,球墨铸铁中还需含有一些合金元素。这些元素以纯金属锭或铁合金方式加入炉中。
表4-6列出几种纯金属的密度和熔点。有一些元素熔点较低,沸点高,直接加入铁水就能熔化,不会过度氧化,无需制成合金。表4-6中所列镍锭、铜锭都是如此。
表4-6 纯金属熔点和密度

表4-7列出常用铁合金品种、合金元素质量分数范围、熔点。硅、锰和铬虽然都已制成铁合金,但在配料需要时,也可直接把它们加入铁水。
表4-7 各种铁合金成分范围和熔点

续表

难熔铁合金可在初次装料时加入炉中。一般铁合金则在炉料熔化达3/4左右时加入。精细调整成分所需的铁合金应在扒除炉渣后加入。
铁合金一般应破碎至50~80mm块度,并筛除细粒。加入前需要预热。潮湿的铁合金不可加入铁水,以避免铁水飞溅伤及操作者。
常用铁合金的烧损率列于表4-8。镍、铜锭不易氧化,其回收率接近100%。但有时会被卷入炉渣,出现少量损耗。
表4-8 常用铁合金的烧损率

4.1.7 铁水炉前检验
(1)快速金相检验 炉前处理完毕后,从铁水包中取铁水浇注φ25mm试棒。待试棒冷却凝固后淬入水中。抛光后在显微镜下观察磨面(100×)。如试样淬水冷却球径太小难以辨别,可放大到200×观察磨面。此项检验只用于炉前检验石墨球化情况,不用于评定整个铸件质量。
(2)三角试片检验 三角试片如图4-5所示。试片在干坭芯铸型中浇出。待表面呈暗红色淬入水中。冷却后观察断口,测量白口宽度。球化良好的试样表面均有缩沉,断口细密,呈银白色,中心有缩松,尖端白口清晰。敲击发出金属声。此试验可探查球化情况,基体中碳化物存在情况。特别是用于检测孕育处理质量,效果最明显。图4-5显示处理前(左图)及锶硅铁处理后(右图)试片断面。试片白口宽度没有统一规定,应按所浇注铸件厚度和现场积累的经验判断。

图4-5 三角试片
(3)光电直读光谱仪分析铸件化学成分 当前炉前快速分析多采用光电直读光谱仪。这种仪器智能化程度高,只要选择和调整好光道数量、分析元素含量范围、分析线和内标线,就可以同时准确快速测定多种元素含量,包括微量元素含量。
光电直读光谱仪分析过程比较简单,只需在炉前浇注φ20mm试棒,把断面磨光、抛光后,放在仪器上即可进行分析。分析时间很短,非常适用于球墨铸铁炉前快速分析。
4.1.8 感应炉熔炼电耗
感应熔炼电能消耗量较大。在熔化工作中设法节约电能是铸造厂一项重要工作。感应炉设计和使用上都有很大节能空间,下列几方面值得铸造工作者注意。
(1)供电 与熔炉配套的供电变压器应尽量选用较高的输出电压,以便降低输出电流,减少整个供电系统的铜损。例如向工频感应炉供电的变压器输出电压由380V提高到650V,供电系统的铜损可降低30%。
(2)冷却水 要对感应器冷却水进行处理,避免结垢,结垢降低感应器散热能力,减少循环水流通面积。感应器铜管可能因结垢而过热,甚至造成事故,增加电能损耗。
(3)炉衬 炉衬与感应炉的电能消耗关系很密切。操作者应按照规定厚度捣筑坩埚底部和炉壁。较厚的炉底和炉壁会降低电功率输入,影响炉料和铁水的加热速度,使整个熔炼时间延长,电能损耗加大,熔炉生产率降低。表4-9列出感应炉容量与坩埚合理壁厚。
表4-9 感应炉容量与坩埚合理壁厚

注:d为坩埚平均内径。
(4)生产组织 为了减少熔化电耗,应该尽最大可能组织熔炉连续作业。连续开炉与间断开炉相比,电能节约可达10%以上,是节能方面的重要措施。
铁水的温度管理也是节能的有效措施。在炉料熔化和铁水升温阶段要输入较大功率,使铁水温度尽快达到出炉温度。缩短浇注时间对节能也十分有利。接近出炉温度时测定铁水温度,达到出炉温度时要及时出炉。铁水在1300℃加热到1500℃,铁水每升高100℃,每吨铁水的电耗增加35~45kW·h。因此,在出炉前的高温阶段要力争提高升温速度。
延长炉衬寿命有显著的节能效果。因此,要选用优质耐火材料、按合理工艺仔细进行捣筑和烧结炉衬。合理装料和熔化,都能延长炉衬寿命。经验告诉我们,这些方面的付出,都能在延长炉衬寿命方面得到经济补偿。
表4-10列出无芯中频感应炉合理能耗指标。
表4-10 无芯中频感应炉能耗指标

4.1.9 感应炉熔制合成球墨铸铁
以废钢+增碳剂+铁合金作为主要炉料在感应炉或电弧炉中熔制的铸铁常被称为“合成铸铁”。世界上许多国家,钢铁工业及机械制造业产生的大量边角余料以及汽车、船舶等报废后拆解下来的钢料数量很大,这些废钢为生产合成球墨铸铁提供了有利条件。工业发达国家已有相当多的铸造厂采用这种方法熔炼球墨铸铁原铁水。
表4-11所列数据比较了冲天炉铁水(以生铁为基本炉料)和合成铸铁铁水(以废钢为基本炉料)制成的镁球墨铸铁力学性能。
表4-11 两种球墨铸铁性能比较

由表中所列数据作比较,成分近似的合成铸铁水制取的球墨铸铁拉伸强度、伸长率、硬度都稍高于冲天炉铁水制取的球墨铸铁。
合成铸铁必须使用增碳剂提高含碳量,使铁水中碳的质量分数达到球墨铸铁要求。常用的增碳剂有石墨型及焦炭型两种类型,其化学成分见表4-12。
表4-12 增碳剂化学成分

为了增强合成铸铁原铁水的石墨化能力,最好选用石墨增碳剂。这类增碳剂含碳量高,具有多孔隙结构,碳在铁水中容易被吸收;含氮量及含硫量均较低。更重要的是石墨增碳剂具有与铸铁中石墨晶体相同的六方晶格结构,因此能有效地增加铁水中石墨晶核数量,促进合成铸铁石墨化,增碳速度和碳的吸收率均优于焦炭型增碳剂。最佳的石墨增碳剂是经过高温提纯处理的石墨。电弧炉使用的石墨电极在成型时为了改善强度加入一定数量的黏结物质,影响增碳剂纯度和增碳效果。
增碳剂的粒度对于碳的吸收率和增碳速度都有影响。使用石墨增碳剂时,增碳剂粒度以1~4mm尺寸的粒子增碳效果最好。使用前要筛去破碎后存在的细粉和超过5mm的粗粒。根据试验,细粉和粗粒都降低碳溶入铁水的速度。
增碳剂应随炉料分批加入炉中。在炉料加入量达到80%时,将所需的增碳剂添加完毕。含硅量较低的铁水,碳的吸收率较高。因此铁水增碳之前,不宜加铁合金调节含硅量。
在3T中频炉进行的试验表明,经过增碳后,预期含碳量不超过4%时,经过筛选的石墨增碳剂中碳的正常回收率可达到90%~98%,加入增碳剂后应适当加大炉子输入功率,尽快提高铁水熔化速度,以避免增碳剂卷入炉渣,造成损耗。