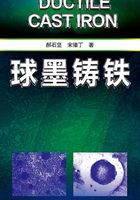
4.2 冲天炉熔炼
冲天炉是熔化铸铁的传统设备。具有筒状结构。图4-6示意地显示炉内燃料、炉料、炉气、进风口、装料口以及炉内的温度分布。

图4-6 冲天炉内燃料、炉料、进风口、装料口以及炉内的温度分布
冲天炉的燃料通常为焦炭(有些炉子采用天然气)。熔化开始前先在炉内装入一批焦炭(底焦),底焦高度根据炉内径而定。底焦上分层交替加入炉料和层焦。鼓风由风口进入,促使底焦燃烧。并逐渐加热与焦炭接触的炉料使之熔化。熔化的铁水由炉缸最下端的出铁口或前炉中流出。
鼓风机通过风口向炉内送入空气,帮助焦炭燃烧。空气中的氧与焦炭中的碳发生以下反应:
(4-2)
(4-3)
反应(4-2)放出的热量使炉料熔化。由图4-6可以看出,风口以上不远的区域内炉温最高,可达1800℃,称为过热带。CO2气体向上流动时,不断与底焦区的焦炭接触,使式(4-3)的吸热反应向右进行,导致炉气温度下降。距风口越远处,炉气中的CO浓度越高。于是沿炉身高度,CO2浓度经过一个最大值后逐渐下降,直到超过一定高度后,两种气体浓度开始保持相对稳定。
鼓入空气中的氧也是在风口平面内浓度最高,但因式(4-2)反应消耗了氧,使氧的浓度逐渐降低。熔化带以上的炉料和燃料,被炽热气流所预热(此范围称为预热带)。预热带接近装料口,装入炉内的炉料首先进入预热带,在此区域被预热到300~500℃,然后在下降过程中,逐步加热、熔化、过热,熔化的铁水储存在最底部的炉缸内或流入前炉。
在冲天炉内熔化球墨铸铁原铁水,除了要求达到预期成分外,更主要的是铁水有足够的温度,尽可能低的含氧量和含硫量。
制取球墨铸铁需要高温铁水。为提高铁水温度,除了改进熔炼工艺以外,改进送风方式是有效方法。最常采用的措施有:预热送风、富氧送风、除湿送风。
预热送风通常是使鼓风通过预热器加热到300℃以上,高温气流加快氧与燃料反应,强化焦炭燃烧,使炉温上升,提高铁水过热温度。此外还能减少元素烧损,有利于脱硫。当预热温度达到450℃以上,效果更加明显。在送风中加入氧气,相对减少炉气中氮的浓度,同样能强化燃烧反应,提高炉气温度和铁水温度,并减少燃料消耗,提高熔化效率。除湿送风可减少气流中所含水蒸气,防止水在高温下分解产生吸热反应降低炉温。也是提高铁水温度的有效措施。
熔炼球墨铸铁原铁水时正确选择炉料是重要的。最好使用国家标准(GB/T1412—2005)所规定的球墨铸铁专用生铁。如受条件限制不能满足要求,至少需用化学成分比较接近的低磷、低硅生铁。
选择冲天炉所用焦炭应注意固定碳和灰分含量,含硫量和水分。固定碳应在85%以上,灰分应小于10%。硫是决定铁水含硫量的主要因素。优质焦炭含硫量应少于0.6%,熔炼球墨铸铁原铁水时最好采用这种焦炭。
4.2.1 铁水成分在冲天炉熔化过程中的变化
熔炼过程中铁水成分发生的变化大部分取决于铁在炉内的氧化与还原反应。而氧化与还原反应则与燃料的燃烧状态、燃烧产物在炉内分布以及与炉气与铁的接触状态有关。
在冲天炉内已经熔化的铁水流过过热区时,以及在熔化区、炉缸内铁水都和焦炭直接接触,焦炭内的碳溶入铁水,使铁水增碳。碳增加量取决于这两种反应的强弱。
采用灰分少、固定碳含量高、块度适当、炉渣熔点低以及铁水与焦炭接触时间长,焦铁比高,热风温度高,炉缸深,石灰石加入量多都能促进铁水增碳。炉气中的O2和CO2与铁水中的C反应,或者铁水和炉渣中FeO与C反应都生成CO逸出铁水,会使铁水减碳。因此,铁水和炉渣中FeO含量较高,脱碳反应易于进行,碳量降低较多,降速较快。此外,炉渣碱度高、FeO活性强;鼓风量大;底焦过高;风口排数与氧化带范围大,则增强脱碳能力。
炉内铁水含碳量在熔化过程中自动变化。铁水碳当量为亚共晶时,成分变化趋势是增碳。碳当量为过共晶时,变化趋势变为减碳。一般认为,冲天炉熔炼过程中碳质量分数的变化是趋向于达到共晶成分。
硅和锰含量的变化也取决于炉料氧化与还原过程。酸性冲天炉熔化期间,炉内气氛基本上是氧化性的。在熔化带、过热带与炉缸内铁水与炉渣接触,炉渣中的氧化铁以及铁水自身所溶解的氧都能使硅和锰受到氧化,增加炉渣及铁水内SiO2和MnO含量。炉气中存在的O2、CO2以及炉渣中的FeO、铁水中的溶解氧都能使硅和锰氧化而烧损。
炉气中含有CO和CO2两种气体成分。当鼓风量较大,焦炭燃烧完全,生成CO能力较弱,CO2在混合气体中的体积分数增加,即“燃烧比”增加,可使炉渣碱度提高,硅的烧损率增加。
酸性冲天炉熔炼过程中,硅和锰烧损率分别约为10%~20%及15%~25%。碱性冲天炉熔炼时,硅增加到20%~30%,锰减少到低于10%~15%。
酸性冲天炉熔炼球墨铸铁时应尽量减少铁水增硫。增硫主要原因是焦炭中的硫转入铁水。冲天炉所用冶金焦炭含硫量一般约为0.6%~0.8%。焦炭中的硫约有90%在炉中与碳化合,形成CS2。CS2极易分解,在氧化性炉氛中转化为SO2而进入炉气,SO2在预热带温度下,即与炉料表面反应产生渗硫层。氧化较重的炉料渗硫量较多。可使炉气中的硫转入铁水。其余的硫与钙、铁等化合成FeS、CaS或以CaSO4、FeSO4等硫酸盐形式存在。FeS促使铁水增硫。渣中的CaS与FeO生成FeS进入铁水也能增硫。炉气中这两种方式的增硫量约占总增硫量60%。
焦炭含硫量高、块度小、加入量较多时,铁水增硫量增加。炉渣碱度高,则脱硫能力强。球墨铸铁需要低硫原铁水,在炉壁抗炉渣侵蚀能力范围内,炉渣碱度应较高。
渣中FeO含量增加时,降低炉渣脱硫能力。提高炉温有利于炉渣脱硫。在提高炉温方面,不能单纯依靠增加燃料量,采用预热送风是比较有效的措施,我国一些生产球墨铸铁的工厂使用热风、碱性水冷冲天炉取得很好的效果。
铁水中的锰有脱硫能力。锰与FeS化合生成MnS。MnS进入炉渣而使铁水含硫量降低。也消耗了一部分锰。为脱硫而需加入的锰量可按下式计算:
ω(Mn)=1.73ω(S)+0.3
酸性冲天炉中内,铁水中的磷几乎不会被氧化而脱除。在炉料熔化前后含磷量变化很少。碱性冲天炉熔炼可使铁水中的磷量降低。但炉温高对脱磷不利。
冲天炉熔炼时需要向炉内大量鼓风。鼓入空气中所含氮与高温铁水接触,会显著提高铁水的含氮量。炉温高使溶入的氮量增多。制取高韧性铁素体球墨铸铁需要注意这个问题。
除了炉料带入的氮以外,还有一些情况能增加铁水含氮量。
①以氮气为载体向铁水喷射脱硫剂。例如,高碳低硅铁水以此种方法脱硫时,铁水的含氮量由0.0070%~0.00995%增加到0.0188%~0.0164%。增氮量与铁水温度,处理时间和喷射压力有关。
②用于造型和制芯的合成树脂黏结剂(例如呋喃Ⅰ型树脂、糠醇改性脲醛树脂)氮含量很高,有的ω(N)>10%。如果铸件清砂时未把表面残砂清理干净就作为回炉料使用,将会带入氮。有些铸件含有氮气孔,也会使铁水增氮。
③采用废钢和增碳剂生产球墨铸铁原铁水时,需加入较多石油焦炭等增碳剂。这些物料含氮量都比较高,甚至可以达到0.6%,在高温下这些氮极易溶入铁水,增加铁水中含氮量。
4.2.2 合金元素的烧损
合金元素在冲天炉熔化过程中的损耗率见表4-13。
表4-13 合金元素在冲天炉熔化过程中的损耗率

①以钒钛生铁形式加入。
4.2.3 炉渣控制
冲天炉熔炼过程中,焦炭燃烧后产生的灰分、炉料表面沾附的泥砂和锈蚀物、炉衬被侵蚀后残留的耐火杂质,都会影响冶金过程。为使这些杂质排出炉外,需要向炉内加入熔剂,熔剂与上述杂质形成具有一定流动性的炉渣,便于从炉内排出。
炉渣另一重要作用是可以清除焦炭燃烧后表面灰烬,焦炭与铁水接触面增加,促进铁水增碳,又促进焦炭燃烧。更重要的作用是控制和减少铁水中元素的氧化减失,提高元素收得率。获得含氧量低、化学成分准确、质量稳定的铁水。
组成熔剂的造渣材料主要是石灰石和石英石。石灰石(CaCO3)在炉内高温下分解为CaO+CO2。CO2随炉气排出,CaO成为炉渣的碱性组分。石英石(SiO2)是炉渣的酸性组分。炉渣以两类组分的质量分数(%)比值划分为酸性渣和碱性渣。其组成物典型含量列于表4-14。
表4-14 炉渣组分

对冲天炉冶金过程有影响的炉渣主要技术指标有:碱度、熔点与流动性、FeO含量。
碱度(A)是碱性化合物与酸性化合物的质量分数比。SiO2、P2O5为酸性化合物,Al2O3为中性化合物,CaO、MgO、MnO、FeO为碱性化合物。碱度A通常以(CaO%+MgO%)/(SiO2%+Al2O3%)表示。CaO和SiO2是炉渣主要组分。为计算方便,碱度(A)也可简化为CaO%/SiO2%比值。A<0.8为酸性炉渣,A=0.8~1.2为中性炉渣,A=1.2~1.5为弱碱性炉渣,A=1.8~2.55为中碱性炉渣,A≥2.5为强碱性炉渣。调整两种化合物比值,可改变炉渣碱度。
碱度对炉渣性质及炉内的冶金反应有影响。日常需要对炉渣进行例行化验。还可以观察炉渣外观大致判断炉渣碱度。
炉渣碱度对铁水质量有显著影响。炉渣碱度高,FeO含量低,脱硫能力增强。碱度高增加硅烧损。但锰的烧损减少。碱度较高、炉渣过稀、炉渣量过多都会加剧炉衬的侵蚀,缩短炉衬寿命。
炉渣中FeO含量高,炉渣氧化活性增强,铁水中碳、硅、锰的氧化烧损增大,硫含量增加。一些合金元素也因FeO的氧化作用而遭损耗。
控制炉渣质量通常需要化验其中的FeO、CaO、SiO2。这些化合物的质量分数可作为评定铁水质量的数据。但是在熔炼过程中,因化验时间较长,来不及根据化验结果调整炉渣,常需采用快速炉前检验方法来评定炉渣质量。
黄绿色玻璃状炉渣表示炉况正常,熔剂配比和加入量合适。
刚从放渣口排出的黑色熔渣为酸性渣,高温状态可拉成丝。
弱碱性渣凝固后呈玻璃状,随着碱度提高,逐渐显示无光泽的黑色、黑褐色、暗灰色。显示多孔外观,刚出炉时拉不成丝。
碱性渣多呈黄色或灰白色,断面多孔。
强碱性渣(碱度大于2.5)较轻,出炉后逐渐变为乳白色,断面多孔,冷却后自动粉碎成粉末。当碱度A>3.5冷却后变为灰白色的粉状物质。
含硫较多的炉渣显深咖啡色,呈疏松状,随后变黑并发泡。发现此种炉渣后,应及时放出部分炉渣,以防止铁水回硫。并重配渣料,造弱碱性炉渣。并适当提高炉温。
炉温低、铁水氧化严重时,炉渣为黑色玻璃状,铁水表面呈白亮色,不断出现很厚氧化皮,流动性差,三角试片白口增加,含气量试样出现气孔。硅、锰已经大量氧化烧损,此时应适当增加层焦质量,提高炉温,还原FeO。
炉渣熔点定义为渣能自由流动的最低温度。也显示渣的黏稠度。中碱性炉渣正常的熔点约为1300~1350℃。此时炉渣容易和铁水分离。为提高炉渣流动性,应提高炉温、适当增加FeO含量、减少造渣材料中石灰石加入量(渣中碱性氧化物质量分数减少)。但FeO含量增加,渣的氧化性增强,炉料中的元素的烧损量增加。另外碱度过高和过稀的炉渣都会加剧炉衬侵蚀,缩短炉衬寿命。
造渣材料随层焦加入炉中,加入量通常是层焦质量的25%~30%。